Vic Coil Style 1
Here you will find information about Vic Style 1 parts and kits
More wire does not necessarily mean more voltage. In fact more wire increases the copper losses of the coil which reduces efficiency. The problem I see with that core is the core area is so small it puts a limit on maximum volt-seconds the core can handle without saturating.
If you have a larger area core or use a different core material you can reduce the total size of the vic, decrease the amount of wire needed to achieve specific inductances, increase the output voltage, and increase the efficiency as well as produce better output waveforms (reducing the amount of wire and turns is an easy way to minimize parasitics).
Stanley Meyers 5-Coil VIC Transformer
Winding and Wire information
After studying existing material on Stanley Meyers 5-coil VIC transformer, a friend of
StanleyMeyerWebshop has written a MATLAB program to fit measured values of DC resistance,
induction values and bobbin dimensions, to reach some practical value of the numbers of windings
and the wire diameter. Parameters to fit were, number of turns, wire diameter and air-gab.
Calculations revealed that two columns of the measured data was swapped for some reason. Here
are the resulting values based on a ferrite core with a relative permability of 2000:
Unit Feedback Primary Secondary L1 L2
Windings 487 629 3384 3558 3290
WireDia[um] 229 269 254 254 254
WinHght[mm] 2.6 1.4 6.6 6.9 6.4
L[mH] 25 42 1203 1330 1137
error[%] 4 -0 15 5 -0
WireLen[m] 27 35 213 225 206
Airgab[mm] 3.2
Ueff 71.8
Enamel-insulated 0.25mm Ø copper wire vill be used:
http://dk.farnell.com/pro-power/ecw0-25/wire-1120m-1-0-25mm-coppertransprnt/dp/1230976?Ntt=1230976
The original wire diameter seems to be slightly thicker but the number of turns is the most
important parameter. When putting on the windings it is recommended to put a layer of insulating
tape every other layers. This provides insulation between layers as well as a smooth surface to lay
the next windings on. Space is tight on the secondary windings. When starting on the winding, put a
piece of insulating tape on top of the start of the wire, so that extra insulation is provided against all
other winding layers.
The insulating tape could for example be 15 mm polyimide (kapton) tape:
http://dk.farnell.com/jsp/search/productdetail.jsp?sku=1503251&CMP=i-bf9f-00001000
When attaching the tape, make sure that there is minimal amount of overlap (if more tape pieces are
needed per layer) and make sure that it is not in the same place to prevent humps from which the
wire will slide down from.
With 0.25 mm wire there is space for approx. 110 turns per layer.
Feel free to use this information for experimentation. PDF here www.stanleymeyermedia.com
Thanks and all the best,
Per Ritter
RE: Water Fuel Injection System Memo WFC 425
Page 6-37
Tri - Coil Construction
Resonant Choke Coils are composed of 430F or 430FR inductance stainless steel film coated wire (typically .004 Ga. Or smaller) which are axially Bifilar wound about core bobbin, forming individual spiral-wrap electrically connected in sequential order to form resistive pickup coil.
Primary Coil (typically .030 Ga.) film coated magnet wire is longitudinal wrapped in space relationship on top of and layered bi-directional across spiral-wrap coils to complete bobbin cavity.
Secondary pickup coil is, also, composed of individual spiral wrapped coils (typically .002 Ga. magnet wire) electrically connected in sequential order to form bobbin cavity, which is placed on top of, and in space relationship to primary coil cavity
RE: VIC Matrix Circuit Memo WFC 426
Page 7-5
Inductor and Inductor is wound or coil-wrapped in such a manner as to increase the magnetic flux intensity of coil-wrap. The circular-spiral turns of wire is separated by an Insulated Dielectric Coating Material which forms a series of capacitors when magnetic flux-lines produces Electromagnetic Coupling Field during pulse on-time. The series resistance value is determined by ~e composition of the wire material in terms of its ohmic value per given length and diameter cross-section: Resonant Charging Chokes 430F/FR 36 A WG (.006)stainless steel (s/s) wire
Page 7-6
equals 60 micro ohms per centimeter; Primary Coil 22 A WG (.028) copper wire equals 5.1933 ohms per pound weight; Secondary Pickup Coil 35 A WG (.007) copper wire equals 13K ohms per pound weight. "Pyre-ML" trade name "Himol" polymer coating-material is used to impart thermal and mechanical resistance to the stainless steel (s/s) wire (614/615) coating; both magnet wire sizes uses solderable Nysol (Polyurethane Nylon Jacket) insulation enamel coating as a electrical shield-material ... all dielectric coatings having an effective 3KV per mil dielectric value and formulated
specifically to endure automotive temperature range from _ 40 0 to 1550 C.
An I-core is sufficient if the magnetic fields of both chokes cancel eachother out,
Page 7-14 also talks about closed loop 53 of fig. 190.
VIC Bifilar Wrap Coil-Assembly (10-3B) and VIC Dual Coil Wrap-Assembly (10-3A) both utilize either
"E"& “I” and "U" Inductance Core configurations to concentrate Mutual Inductance Fields (Rp l/Rp2) in order
to optimize Amp Inhibiting Process. "E" “I” core shape (10-3B) is most preferable since amp spike surge is
minimize during repetitive pulsing operations.
30 GUage Wire
with gap on core 2000 permability on ferrite core matches dons readings.

Meyer had 10 of these units
running in series onto the 11 cell electrolyzer.
the extra cell was on a diferent cicuit for heating water in freezing conditions.
-
Yellow is Pick up coil feed back
-
Green is Primary Transformer
-
Blue is Secondary Tranformer
-
2 red are the chokes ( May be same or slightly diferent winds.)
The chokes, power coils, etc.. in Meyer's circuits seemed to have always been very confusing to many people. More people today are understanding how the chokes were designed by simply reading the tech brief that has been under all our noses the whole time.
Several people in the The H2earth Institute - A Virtual Center of Excellence in Waterfuel Technology such as Josh and others are looking at this very closely. I was surprised to find so many ideas about how the chokes are designed considering the fact that the text descriptions and diagrams in the WFC tech brief are very, very clear.
Upon further examination, these are my comments, which may be right or wrong, I don't know but they make sense to me
Here is the tech brief on the wfc by Meyer:
http://www.esmhome.org/library/stan-...ical-brief.pdf
Below are a few tidbits from the tech brief on the bifilar, arrangement, purpose, construction, specs, etc...
Page 6-3
"Resonant Choke Coils (56/62) of Figure (3-23) (Memo WFC 422 DA) are composed of 430F or 430FR inductance stainless steel film coated (hi dielectric value) wire (typically .004 Ga. or smaller) which are axially (spiralled) Bifilar wound about core bobbin (502), forming individual spiral-wrap (inner to outer circumference and being equally-length) coils (501a xxx 501n) electrically connected in sequencial order to form resistive pickup coil (503)."
choke #56 is drawn incorrectly - they are wrapped in the same direction. I'll get to that later.
from page 7-5
Both Inductors (LI/L2) are Bifilar wound in equal length to optimize the electromagnetic field strength (FL) in equal electromagnetic intensity (FLI = FL2) to encourage and promote "Electron Bounce" phenomenon (700) of Figure (7-9) while adjusting (programmable pulse wave-form) input signal Pulse-Frequency (49a xx 49n) to "tune-in" to the "dielectric property" (Re) of water (85) ... causing amp flow to be reduce to a minimum value while allowing voltage potential (627) of Figure (7-7) to go toward infinity if the electronic components would allow it to happen, as graphically illustrated in (750) of Figure (7-14).
page 7-11
"each choke-coil (LIIL2) being of the same impedance value since both coil-wraps (56/62) are Bifilar wound together onto a single spool-bobbin,"
page 10-1
"The Amp Inhibiting Circuit (970) of Figure (10-1) as to (690) of Figure (7-8) is composed of two copper wires "Bifilar" wound (wrapped) about a magnetic induction core to allow amp restriction (minimizing current leakage) while encouraging "Voltage Potential"(Va xxx V n) across the water molecule to perform WFC "Electrical Polarization Process", as so illustrated in Figure (7-1) WFC memo (426) titled VIC Matrix Circuit."
page 10-2
"VIC Bifilar Wrap Coil-Assembly (10-3B) and VIC Dual Coil Wrap-Assembly (10-3A) both utilize either "E"& “I” and "U" Inductance Core configurations to concentrate Mutual Inductance Fields (Rp l/Rp2) in order to optimize Amp Inhibiting Process (750) of Figure (7-14). "E" “I” core shape (10-3B) is most preferable since amp spike surge is minimize during repetitive pulsing operations."
page 10-4
"Increasing energy-yield (16/gtnt) still further (xxx 16/gtntnl+ 16/gtntn2 + 16/gtntn ... etc.) is accomplished by increasing the number of Resonant Charging Choke Stages (xxx 56/62n + 56/62n 1+ 56/62n2 + 56/62n ... etc. -S- xxx SS56/62n + SS56/62nl + SS56/62n2 + SS56/62n ... etc.) of Figure (10-4) in "Sequential Order" ( -S-) since the total number of Multi-Coil Magnet bifilar coils (56/62a xxx 56/62n) serially electrically connected together are sequentially electrically linked to an equal number of serially electrically aligned Stainless Steel Resonant Coils (SS/56/62a xxx SS/56/62n) ... allowing eachlboth bifilar coil assembly (56/62a xxx 56/62n -SSS56/ 62a xxx SS56/62n) to be electrically and magnetically energized in the same progressive direction toward Water Gap (Cp) and away from blocking diode (55) of Figure (3-34) as to Figure (10-1) and Figure (10-3) '" keeping amp-surge (inhibiting amp flow) to a minimal level [See Voltage Performance Graph (750) of Figure (7-14)] while enhancing Voltage Potential of Electrical Stress (64/RU-RU'a xxx 64/ST-ST'n) as additional Dual Choke Coils (56/62 _ SS56/62) are included in the stacked coil-array forming Voltage Intensifier Circuit (970) of Figure (10-1) as to (620) of figure (7-1) ... see Dynamic Voltage Waveform (770) of Figure (8-1), once again."
above pic if only you want to put more bifilar chokes in series
pages 10-4 and 10-5
"The magnet Coil-Wire (56/62) is best suited for Voltage inducement while the inductance/capacitance/resistance properties of Stainless Steel coil-wire (SS56-SS62) is appropriately used to restrict electron movement beyond the self-inductance of each energized coil when elevated voltage levels (up to beyond 40 kilovolts) are to be reached/obtained without experiencing any appreciable amount of "Amp Influxing." Generally, magnet coil-wire length is longer than the Stainless steel coil-wire length and magnet bifilar-coil (56/62) is placed on top of Stainless Steel bifilar-coil (SS56/62) to maximize mutual inductance coil-field (Rp2) (adding Rp1 +Rp2) of (690) of Figure (7-8) to cause coil capacitance (Cda xxx Cdn) to help maintain and even increase pulse voltage amplitude (xxx Vn + Vn 1 + Vn2 + Vn .... etc.) while the resistive value (Rs2) of SS Coil-Wire (SS56/62) performs the work of further resisting the flow of amps not inhibited by both self-Inductance fields (Rpl + Rp2), as so illustrated in (690) of Figure (7-8). In all cases, bifilar coils (56/62 - SS56/62) are electromagnetically orientated in the same direction."
The above pic I drew shows the bare bones bifilar choke system.
Top is the secondary transformer coil.
Output through blocking diode goes into one of the bifilar choke winds.
In figure 10-3B, it is easy to see that the direction the winds are coming off the core that when the positive hits that coil, north is at that side.
The potential follows through to the outside positive tube through water to negative inside tube.
Positive potential moves to the other bifilar choke coil (wound the same direction) meaning that north will be at THAT end (opposite of the north on the other coil) and through this coil and to the negative on power supply.
Both choke coils on the pos and neg tube create opposing magnetic fields against each other. On the on pulse, the pos side choke coil is north by the diode side and south by the pos tube side... the neg side choke coil is north by the tube side and south by the power supply neg. On the OFF pulse, they both reverse and also oppose each other.
In many diagrams in the tech brief, this exact configuration shows that the choke coils are in opposition at all times on the off and on pulse.
My picture shows the bare bone system without the electron extraction circuit (EEC) or any coils being tapped.
Meyer says that the I core (rectangle with line down middle) as shown in fig 10-3B is the best core for the choke since this configuration restricts amps the most.
More ..

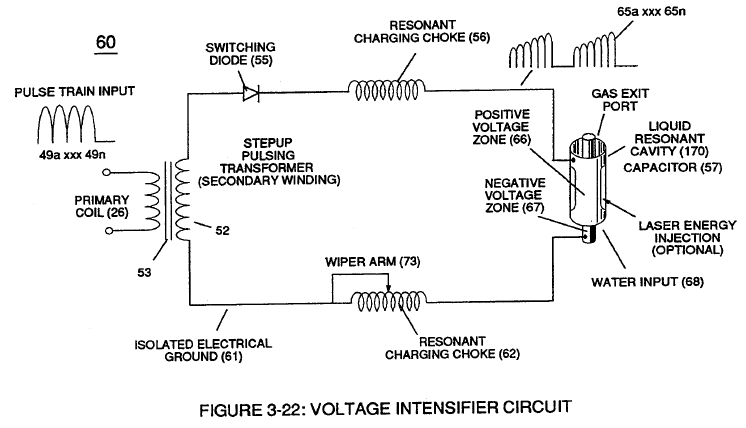

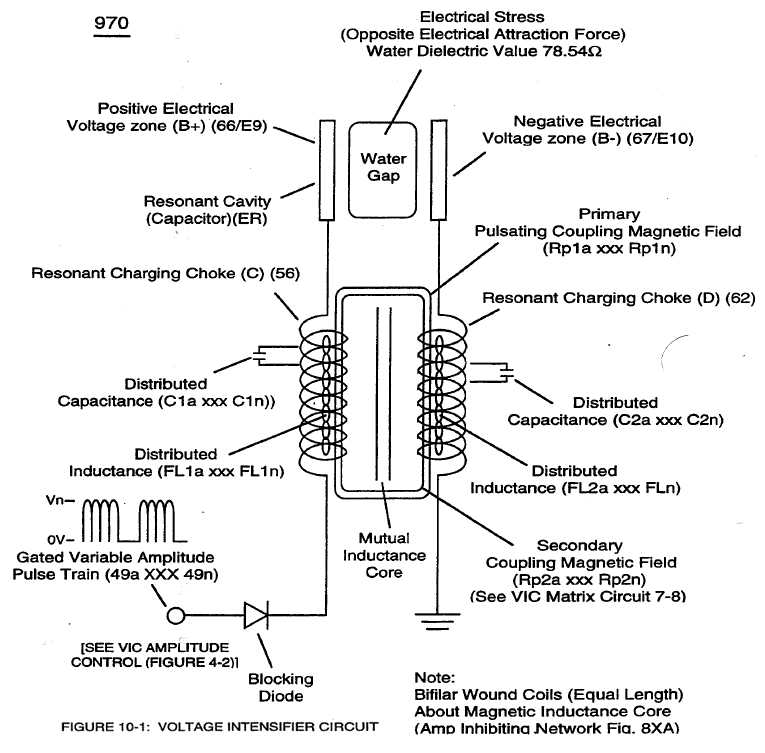

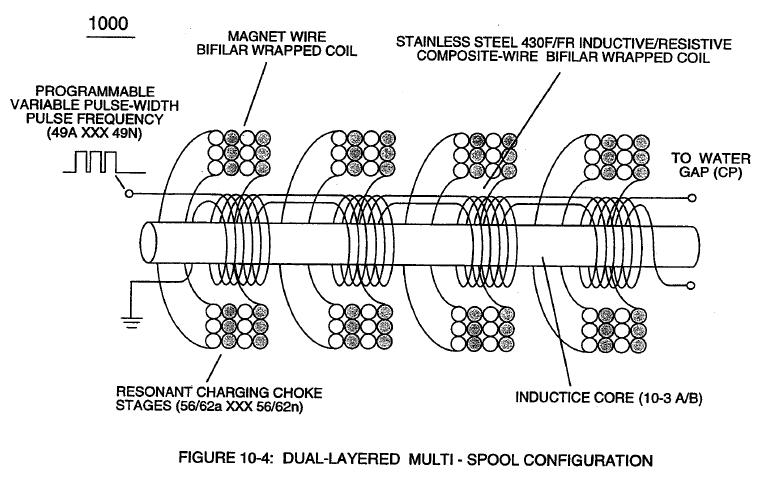