Secure Supply USA
Fueling Healthy Communities
Power Gas Architecture | Developer
Secure Supplies Group

Gas Compressor Systems.
Hydrogen Gas, LPG, Propane, CNG, Biogas.
Secure Supplies partnered and agreed with PDC Machines in 2016 to only specific PDC Equipment and Gas Handling in our proprietary deigns for clients.
PDC is a family owned company and we all at Secure Supplies believe the best Compressor vendor for projects designed by Secure Supplies.
PDC Machines is an ISO 9001:2008 certified company that provides engineered solutions for specialty gas and chemical processing equipment worldwide. PDC 'sstate-of-the-art products are the preferred choice for a variety of industrial/specialty gas, renewable energy, general industrial and petrochemical applications.
PDC earned a reputation for providing reliable compression systems backed by superb world class customer service and technical support.
PDC's compressor systems have minimal maintenance requirements, are easily maintained and are supported by factory inventory of critical, consumable spare parts.
Certifications we Comply with are as follows ;
-
ISO 9001:2008
-
American National Standards Institute, ANSI
-
American Society of Mechanical Engineers, ASME
-
American Welding Society, AWS
-
Canadian Standards Association, CSA
-
Canadian Registration Numbers, CRN
-
CE marked, European Union (ATEX Directive, Pressure Equipment Directive)
-
Chinese, SQL
-
The High Pressure Gas Safety Institute of Japan, KHK
-
Korean Gas Safety, KGS
-
National Electric Code, NEC
-
National Fire Protection Association, NFPA
-
Occupational Safety & Health Administration, OSHA
-
Underwriters Laboratories, UL, cUL
-
Russian certificate of conformity, GOST-R
Ordering is Straight forward simply contact Secure Supplies with your requirements.
Secure Supplies provides you with
a Needs Analysis and Design Development.
-
Gas Diagram Design
-
Flow Rate Design,
-
Pressure Design
-
Purification System Design
-
Cooling system Design
-
Safety System Design
-
Monitoring Design
-
Operation and Maintenance Planning
To order your compressors for your projects Please Contact
Daniel Donatelli
Founder
Secure Supplies
Whatsapp + 66 83 6378 3443

Diaphragm Gas Compressors Explained
A diaphragm compressor is a positive displacement machine which consists of a hydraulic system and a gas compression system. Diaphragm compressors are somewhat traditional in the sense that the hydraulic system uses a linear reciprocating piston attached to a crank shaft that is driven by an electric motor. The hydraulic piston travels through a cylinder which moves a column of oil. This oil is used to lubricate the lower end running gear and to energize the gas process system.
The gas processing system consists of the gas head assembly, three metal diaphragm plates and the compressor check valves. When the hydraulic oil is pumped to the underside of the diaphragm set they flex through a contoured cavity in the gas head as the compressor check valves allow for the process gas to flow in & out of the compressor.
Triple metal diaphragm compressors are unique because they are leak-free and non-contaminating since they do not utilize dynamic seals and the diaphragm set completely isolates the process gas from the hydraulic system. Each compressor also includes a leak detection system that monitors the integrity of the diaphragms and static o-rings. Breaches in these components can signal an alarm and or automatically shut down the compressor.
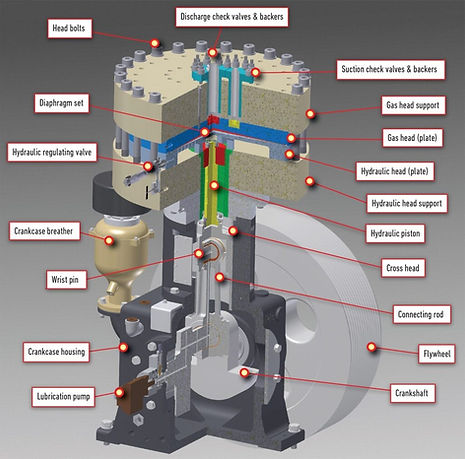

Serving Many Industries
Our leak free and oil free, gas, non-lubricated reciprocating diaphragm compressors are found in virtually every industry worldwide. These include:
Alternative Energy/Hydrogen refueling stations
Chemical and Petrochemical (CPI)
Oil & Gas
Specialty Gas
Power Generation
Pharmaceutical
Semiconductor
Food & Beverage
Research & Development
General Industrial requirements worldwide
Containerization
At the request of our customers, we can package our compressors and customers equipment and instrumentation inside a container.

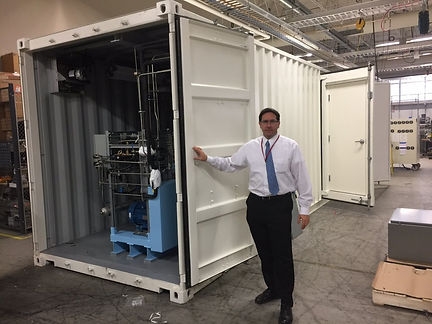
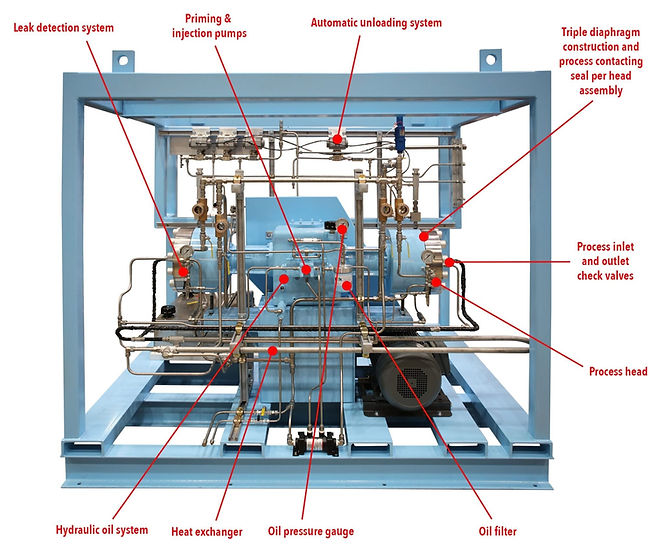
Oil Regulating Valve
The oil relief valve limits maximum hydraulic (and thus gas) pressure and assures that the diaphragms completely “sweep” the upper and lower cavity contours to maximize displacement.
Injection Pump
A plunger type injection system on all motor driven diaphragm units. The injectors are also crank driven and precisely meter hydraulic fluid flow during the operation of the compressor.
Process Head
Factory machines the process heads from a variety of materials for process gas compatibility. 300 series stainless steel is the standard used for most applications.
Process Contacting Seals
We offer an extensive variety of static elastomeric O-ring seals for process gas compatibility, options include Buna-N, Viton, and Teflon encapsulated Viton and Kalrez.
Priming Pump
We provide an automatic, positive displacement gear pump. Priming is crankshaft driven and automatic upon start up. This eliminates priming problems that are typically associated with gravity fed pumps.
Cavity Design
The deflection and resultant stresses in the metal diaphragms are controlled by carefully designed cavity contours. We use state of the art design and analysis tools as well as cutting edge programs to model these.
Process Inlet and Outlet Check Valves
Compressor process check valve design is dependent on operating conditions and the process gas itself. Compressors typically utilize cartridge or plate style check valves. Valves and valve pockets are designed for easy removal and maintenance.
Hydraulic Oil System
The hydraulic system is designed to assure uniform diaphragm deflection, prevent knocks, vibration, cavitation and yield smooth, quiet compressor operation.
Unique oil distribution techniques are employed to eliminate pressure differentials and gradients.
The system utilizes an automatic priming pump, positive displacement high-pressure injection pump and oil relief valve with bypass valve for smooth, easy starting.
Triple Diaphragm Construction
The diaphragm set consists of three plates. The upper or process side, the lower or hydraulic side and the middle diaphragm. The middle diaphragm is brass to preclude galling. The upper and lower are typically 301 SST for most applications. However, the upper diaphragm material can be supplied in alternate materials, such as Inconel 718, for process compatibility.
Leak Detection System
Included with every diaphragm compressor is a leak detection system. This system detects diaphragm or seal failures.
Our leak detection system monitors the gas and hydraulic sides of the compressor and will alarm and or shutdown the compressor when an anomaly is detected.
Proper maintenance, operation and clean/dry process gas promotes component operating life.
Automatic Unloading System
The compressor is automatically hydraulically re-primed at start-up and unloaded upon shutdown. This process is an important procedure which will not only provide for maximum efficiency but also eliminates the need for an operator to start-up/re-prime the compressor.
Safety Interlocks
Features include shutdowns for low suction pressure, high discharge pressure, low oil pressure, low water coolant and diaphragm or O-ring failure. Audible and visual annunciators can be supplied for an added level of protection. The compressor can be completely instrumented for automatic operation.

Why Secure Supplies places these Diaphragm Compressors in our Developments?
Non-contaminating Gas Compression
The triple diaphragm set ensures that the process gas is completely isolated from the hydraulic oil. The compressor does not use dynamic seals eliminating the potential for seal particulate to be imparted to the gas stream. Filters and oil removal systems are not necessary – Hydraulic oil cannot migrate into the process gas.
High Compression Ratio
Our metallic diaphragm compressors can achieve typical compression ratios up to 10:1 for certain models.
Superior & Extended Diaphragm Life
All aspects of diaphragm compressor design are intended to enhance component life, improve operability and reduce and simplify maintenance.Diaphragm cavity contours, which control stress in the diaphragms, are carefully controlled to provide uniform stress distribution. Special manufacturing processing is used on the diaphragm surfaces to enhance fatigue life.
Many of our customers have experienced continuous running times of 10,000 to 40,000 hours between routine maintenance minimizing the need for spare parts replacement.
Variable Suction Pressure
Compressors are capable of sub atmospheric as well as high suction pressures. Compressors can be used in in applications requiring low or high compression ratios. And for applications requiring intermittent or continuous service duty.
Many of our customers have experienced continuous running times of 10,000 to 40,000 hours between routine maintenance minimizing the need for spare parts replacement.
Unique Oil Distribution System
The hydraulic system is designed in such a way as to assure uniform diaphragm deflection, prevent knocks, vibration, cavitation and yield smooth, quiet compressor operation.
Fast Acting Leak Detection System
To detect and indicate diaphragm and seal failure.
Safety Interlocks
The compressor will be completely instrumented for safe and automatic operation.
Environmentally Safe
Our diaphragm compressors use static seals. There is no migration of gas to the crankcase as such the crankcase does not require purging or venting. The gas system integrity is monitored to preclude leakage of gas to the atmosphere.
Safe Compression of Corrosive Gases
We use non-flammable hydraulic fluid and all process-wetted components which are constructed from corrosion-resistant materials for processing of corrosive or oxidizing gases for safe operation and which will prolong the life of maintenance components.
High Discharge Pressure
Gas diaphragm gas compressors are capable of providing discharge pressures to 15,000 psig/1,000 barg and beyond.
Automatic Unloading System
The compressor is automatically re-primed at start-up. Manual start-up requires an experienced compressor technician to be present all the time to re-prime the compressor. Incorrect priming will cavitate the compressor and damage the heads, bolts, diaphragms, o-rings, process and hydraulic system.
Quiet Operation
Below 85 dBA @ 1 meter without sound-proofing enclosure.
Low Maintenance
Typically, only routine oil changes are necessary.
Low Energy Costs
Compressors use a heavy flywheel to provide energy. In addition, Duplex and two-stage diaphragm compressors can be horizontally opposed designs to further reduce horsepower requirements and energy usage.
International Standards Compliance
Diaphragm compressors can be designed and certified to comply with Canadian, European, South Korean, Japanese, North American and other international codes and standards.
ISO 9001 Quality Management
ALL Products and Processes are certified according to ISO 9001 standards for quality management of production and services.
Serving Many Industries
Our contamination-free and leak-tight, diaphragm gas compressors can be applied to:
-
Hydrogen powered fuel cell vehicles
-
Hydrogen powered fuel cell trucks
-
Hydrogen powered fuel cell buses
-
Hydrogen powered back up fuel cells stationary for stationary power generation
-
Conversion of biomass to gaseous hydrogen
-
Hydrogen powered fuel cell material handling vehicles
-
Hydrogen powered back up fuel cells for telecommunication towers
-
Conversion of solar and wind power to hydrogen power (power to gas)

We have an extensive line up of Quality plug and play diaphragm compressors ranging from bare units to fully automated and custom-designed diaphragm compressors with a comprehensive assortment of options to meet any application.

Purity of Inlet Gas
It is critically important that the process gas be clean and dry as it enters the compressor. Suction filters, separators/knockout pots or demisters should be employed at each compression stage to eliminate particulate and or moisture from the gas stream. Gas purity is maintained as it is processed through the diaphragm compressor.
Bare Compressor

Basic Compressor
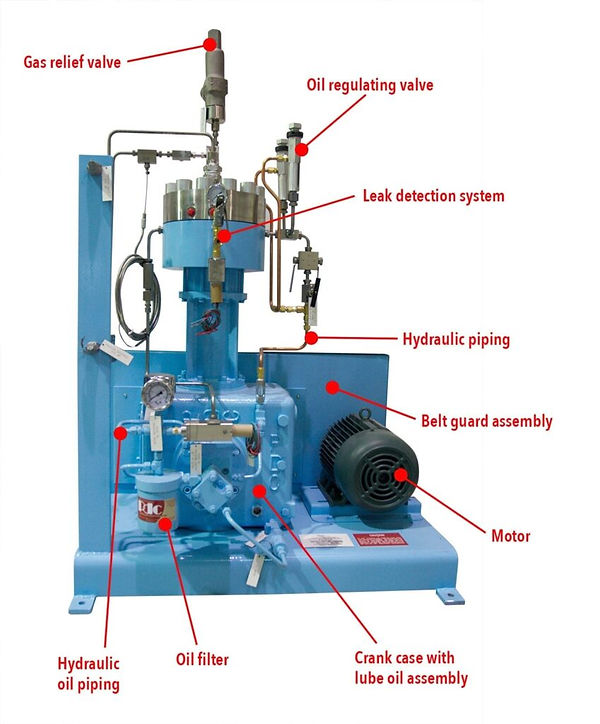
Standard Instrumentation Package

Customized Process Solutions
A customized diaphragm compressor package consists of the standard instrumentation package in addition to a wide variety of piping accessories, instrumentation and controls which are typically defined by the customer.


Hydrogen Dispenser fill station compressor

Hydrogen Dispenser fill station compressor

Hydrogen Dispenser fill station compressor

Hydrogen Dispenser fill station compressor