Stanley MeyerHHO
#Hydrogen #Electric #Generator

Stanley Meyer's water fuel cell - Wikipedia, the free encyclopedia

The World's Smallest ROT Radial Outflow Turbine .
Up to 3 MW that cover 95 Percent of the World's Available Waste Heat,
No Gearbox Needed,
and 6 Month or Less Delivery Time
If you have a specific Industrial Heat Recovery , Engines or Geo Thermal application, we need the temperature in C, and heat flow in terms of btu/hr.
CHP Combined Heat and Power Units
The World's Smallest ROT Radial Outflow Turbine up to 3 MW that cover 95 Percent of the World's Available Waste Heat,
No Gearbox Needed, and 6 Month or Less Delivery Time.
These are Matched to our Prime Power Units and Sold and Installed Separately.
Can fitted from 150 kw to 10 Mw engines.
Also Suitable for Industrial Heat Recovery and Geo Thermal applications.
If you have a specific application, we need the temperature in C, and heat flow in terms of btu/hr.
Radial Outflow Turbine Generator - Organic Rankine Cycle - Turbine
The radial outflow turbine designed and produced by Turbine CNC Company and is for making power from waste heat.
The ROT (radial outflow turbine) operates on a single rotor with multiple stages to direct drive a 50/60 hz AC generator, no gearbox required, and is optimal for Organic Rankine Cycle applications.
Our system makes electricity from heated liquid 80 C to 120 C heat from solar, hot geothermal, engine,
compressor and industrial waste heat.
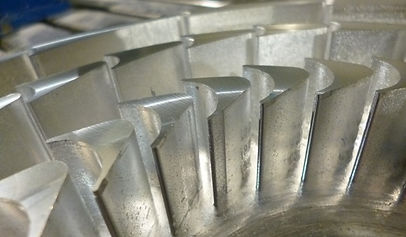


Our turbine peoduction contractor has a Waterjet Machining Center and High Speed Vertical Milling CNC Machine, which allows us to build any size turbine from 5 inches diameter to 24 inches in diameter,
which covers the range from 2 kW to 3 MW in output power.
Low RPM = No Gearbox Needed
The advantage of a ROT turbine is that it is a lower RPM turbine, which allows a direct drive to a standard 1,800 or 3,600 RPM generator. It also allows the use of either 50 hz or 60 hz DC or AC. Pressurized flow enters from the front of the turbine, and is expanded outwards to the perimeter of the turbine through several stages.
Inlet flow is first directed by stators (stationary foils) into the first stage on the rotor, then through another set of stators to another stage on the rotor. The expanded gas exits on the perimeter of the rotor, and finally exits out the back of the turbine.
Because the lower RPM allows a direct drive generator, it eliminates the need for a gearbox which is typical on high speed turbines. The gearbox is added cost, and has to be rebuilt every 3-5 years.
Lower RPM also allows the use of slower speed shaft bearings, which increases the longevity of the the machine operation, and less frequent maintenance intervals.
Low RPM Turbines and Small CHP ORC Systems Can Capture 95 Percent of World's Waste Heat
The prevailing large turbine generator wisdom right now in the commercial market is for high-speed, complex turbines that drive a high speed generator, which requires expensive switchgear and grid-tie equipment.
Philosophy is to keep the technology as advanced and simple as possible, using as much off-the-shelf components as possible to keep costs within a reasonable payback period of 3 years or less.
This cost effective approach will allow more utilization of low grade waste heat, under the 500 kW system size, which we estimate is 95 percent of the worlds available waste heat (that is accessible and available for use).
Very few equipment manufacturers are in this smaller (sub-500 kW) market, because they cannot cost effectively manufacture the equipment, since most of it is custom built using expensive components.
We challenge this conventional market strategy, and present a system that is affordable in terms of a short payback period in electrical production cost savings, from using a low grade temperature waste heat source.
Matching to our Prime Power Hydrogen Fueled Power Plants -Waste Heat Turbine DC Generator System
If you have a diesel engine which is used for power generation, a prime mover such as marine, rail, pumping, compression or other constant use - a Secure Supplies CHP Turbine can capture the exhaust and/or coolant heat to produce power. This may amount to 26 percent additional electrical power output. In addition, you may be able to eliminate the HP used to drive the radiator fans internal or external Fans or electrolyzers.
For example: QSK60-G4 Cummins QSK60 Series Diesel Generator Set 1600KW/1875KVA (1875KVA-2250KVA)
Heat Rejection to Coolant: 850 kWm x 3412 kWm/btu / (30,000 btu/kWe) = 97 kWe available CHP ORC power production
Heat Rejection to Exhaust: 1,180 kWm x 3412 kWm/btu / (30,000 btu/kWe) x 95 percent efficiency = 127 kWe available CHPORC power production
Total Waste Heat to Power ORC Production: 224 kWe
Heat Exchanger from Airec: AirCompact 70 - 160/C
Price Each For Heat Exchanger: Euro 4,500 Ex-works (shipping not included) Sweden.

Electric Generator Power Plant Waste Heat and Geothermal Power Generation Kit
W 24 inch (610 mm)
L 32 inch (813 mm)
H 46 inch (1180 mm).


The turbine system has one moving part. Both the turbine and magnetic rotor are attached to the same shaft, which eliminates any external shaft sealing issues.
The DC power output can be routed to a voltage controller, or to a inverter so that AC power can be supplied to a local or utility grid. A standard solar or wind inverter can be used. Now Offering is now offering the optional SMA grid inverter to convert DC to AC power. Power production can be monitored via web or iPhone.
The entire turbine generator is very durable and designed to last years without any maintenance.
The turbine housing uses standard o-rings for seals, and 3/8 inch bolts for both assembly and mounting bores on the bottom and top of the unit.
The inlet is a 1 inch NPT and the exit is one large 4 inch NPT.
This all-in-one unit can be used in the standard ORC configuration using refrigerants as working fluid, but also with compressed air, steam and other pressurized flows.
Because this is an expander, it can be used in ORC applications, but also in pressure reducing applications, such as natural gas or chiller reducer valves.
The compact size of the turbine generator allow it to be used in stationary but also mobile (transportation) applications.
The modular block design, allows the unit to be dis-assembled, and re-assembled in about less than an hour.
Applications
This unique system allows you to use your Engine Power Plant Exhuast Heat flare gas, waste heat, waste hot water, geothermal, geo-pressurized, hydrothermal, enhanced geothermal, turbine exhaust, or re-injected waste water to power a organic Rankine cycle (ORC) turbine generator.
Geothermal and Waste Heat Organic Rankine Cycle:
The technology developed using a ORC (Organic Rankine Cycle) can operate off any heat source, with a minimum of 125 deg F temperature differential between the heat source and sink.
Geothermal energy is only one potential application. Similar systems are already in operation off heat generated from landfill flares and gas turbine exhaust. Other applications may include using biomass as a fuel.
Why Install a ORC CHP Machine ?
Capturing low grade heat which would otherwise be vented to the atmosphere can be used to generate rotational horsepower. This can be used to power a electrical generator, or other rotary equipment such as pumps. In addition, the exiting, heat from the turbine can be used in CHP (Combined Heat and Power) applications to heat water, desalination, or even in adsorption chillers to make chilled water, ice, or air conditioning.
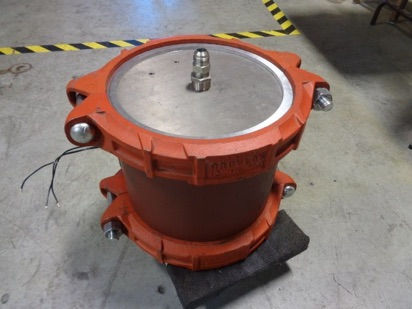
Why Low Temperature Waste Heat ?
Secure Supplies has studied waste heat availability worldwide and has assessed the market to recover that heat which we believe 95 percent is at or below the 100 C (212 F) range. We choose this System of CHP to Simply best the most reliable and cost effictive , made from best components.
Organic Rankine Cycle is more efficient at this range than the Kalina Cycle. For the small amount of the market which has high heat available (well above 100 C) you can use steam systems.
Organic Rankine Cycle uses refrigerants as the working fluid which boil below 100 C (212 F). The pressurized vapor can then be expanded through a turbine to spin a generator.
Radial Outflow Turbine with 15 inch diameter rotor, direct drive to a U.S. Motor 12 kW 60hz induction generator. PLC optional.
If you are wandering about how much power you can generate from your heat source, I need heat flow in terms of btu/hr.
You need to convert hot gas stream into a thermal liquid (water, glycol, oil) which we can then use in our system. To do that, you have to source a HRU - heat recovery unit (or heat exchanger) that takes your heat from your source and converts to a liquid. We have examples of third party HRU sources towards the end of the email (examples are Cain, Bowman and Airec).
What is a CHP ORC turbine generator system ? Organic Rankine Cycle is a way to take low grade temperature waste heat, and make electricity. CHP ORC is a bottoming cycle, specifically designed to utilize low grade heat (80-140 C) and is not very efficient, but can use heat which is otherwise vented to the air.
The process is similar to a steam turbine, but instead of using water as the working fluid to make steam, we use refrigerant, which will turn into a pressurized vapor at a lower temperature than water (100 C). An example of a topping cycle would be using Supercritical CO2, which can be 40-50 percent overall efficiency, but requires very high pressure and temperatures (400 C +).
Who can profit or save money using a CHP ORC system ? While we do build smaller ORC systems, only the larger systems save and make money. Current technology does not cost effectively scale down well, so it is not yet cost effective for residential use. Small business and industrial users can install a CHP ORC system and have a payback in 2-3 years.
What is waste heat, and what heat can be utilized ? Generally, any heat source that can be converted to a liquid (water, glycol, oil, etc.) and is free, is a good source for a CHP ORC system. If you have to pay to harvest the heat (like solar), then it does not make economic sense, unless your grid based power is very expensive.
The CHP ORC system is designed for low grade waste heat recovery, and is only 5-10 percent efficient at the lower tempeatures. If you pay for your heat, or pay to have it harvested, then the payback term will be more than 3 years. Examples of waste heat which can successfully be used in a CHP ORC system, with good payback, is industrial, engine, hot geothermal, biomass heat sources.

Oil and Gas
The oil and gas also provides another possible application for the CHP ORC power plant.
Because most oil and gas wells are quite deep, they are warmed by the natural thermal gradient of the earth. In 2004 the U.S. produced over 2 billion bbl of “waste” water along with the oil and gas production, primarily from the Gulf States with temperatures high enough to produce electricity. This hot water could be used to generate power directly, without impacting oil and gas production. Similar Maps
have been made for South Australian and other Cities Particularys Asia.
Read a .pdf report here - Energy Under Our Feet
Gas turbines used for compressors and power generation provide huge amounts of waste heat. This can be converted to additional electrical power.
To see Gas Turbine to waste heat power options, click here.
Organic Rankine Cycle
The Power Generation TURBINE (turbogenerator) operates using the Organic Rankine Cycle (ORC). The Organic Rankine Cycle (ORC) is similar to the cycle of a conventional steam turbine, except for the fluid that drives the turbine, which is a environmentally friendly low boiling point organic fluid which allow the system to run efficiently on low temperature heat sources to produce electricity in a wide range of power outputs.
The Cycle
The environmentally friendly organic working fluid is turned into vapor by application of a heat source in the evaporator. The organic fluid vapor expands in the turbine and is then condensed using a flow of water in a shell-and-tube heat exchanger (alternatively, ambient air can be used for cooling). The condensate is pumped back to the evaporator thus closing the thermodynamic cycle. Heating and cooling sources are not directly in contact with the working fluid nor with the turbine.
The condenser can use ground source geothermal and air cooled for added efficiency.
For high temperature applications such as Combined Heat and Power (CHP) biomass-powered boilers, high temperature thermal oil is used as a heat carrier and a regenerator is added, to further improve the cycle performance.
Advantages
a. High system efficiency
b. High turbine efficiency (up to 74 percent)
c. Low mechanical stress of the turbine, due to the low peripheral speed
d. Low turbine speed allowing the direct drive of the electric generator without reduction gear
e. No erosion of blades, due to the absence of moisture in the vapor nozzles
f. Long life
g. No operator required
h. Can be service by standard refrigerant technician
The system also has practical advantages, such as simple start-stop procedures, low noise operation, minimum maintenance requirements, and good part load performance.
Applications
a. Low enthalpy geothermal plants, number up small system modules - unlimited plant size
b. Combined Heat and Power (CHP) systems - use condenser cycle to produce hot water for heating, domestic, ice melting, or even through a secondary chiller for cooling
c. Heat recovery applications, such as foundry, process or waste water in oil re-injection wells
d. Solar applications
Modularity
The CHP ORC Turbine Generator consists of a single assembly, or a full CHP ORC system containing all the equipment required for the power skid to be operated (i.e. heat exchangers, piping, working fluid feed pump, turbine, electric generator, control and switch-gear). Larger units are composed of multiple modules, pre-assembled at the factory in optional shipping containers.
Because of that, units are easy to transport and to install, and they are easy to interface with the hot and cold sources on site.
Since they are container mounted, you can stack and tie together horizontally, or vertically. You can even use them on ships.
Perfect for remote operations, like islands.
Secure Supplies
Secure Supplies Turbine provides CHP Organic Rankine Cycle project development services as well as turnkey products and services in the areas of renewable energy technologies and in developing clean power/energy projects that will generate renewable energy credits, like the carbon dioxide credits and emission reduction credits.

Secure Supplies Rapid Technology Uptake Program
Build Your Own Brand with Secure Supplies H2 inside.
Your business support is value to Secure Supplies and we are preapred to pay for it.
The Most important goal to to deploy the technology and teach others how to clean up our air water and world in general.
So If you would like to assemble your own Organic Rankine Cycle Waste Heat to Energy System, Secure Supplies
sells the core of the system, the turbine/expander. Mb + 66 83 647 3443 danieldonatelli1@gmail.com
You can build or purchase the parts and use our plans with consulting to guide you along the way.
Purchase the parts and assemble the system.
This allows you to use locally available components to save on shipping, while giving your the opportunity to build your own brand to sell to your customers.
You may choose to manufacture the necessary components, or purchase them from suppliers. Of course we can sell you the components, or refer you to suppliers. We supply the support, from manufacturing, assembly, start-up commissioning to training.
Using our core turbine/expander, you can stay local or global with your CHP ORC system with the security of knowing that the turbine is standardized. The key component to any CHP ORC system is the turbine/expander. Most of the cost associated with the development and manufacture of CHP ORC systems is with the turbine/expander.
Using this strategy, Secure Supplies haa taking all the years of research and development out of the equation, which allows you to rapidly assemble and deploy your CHP ORC machines to your customers.
Secure Supplies is constantly making its turbine more efficient as well as the design of the ancillary components which make the CHP ORC system work. Some of our technology which leads other ORC manufactures is our implementation of nano-fluid technology which enhances the heat transfer in both the evaporator and condenser.
Using a nano-fluid additive makes the system more efficient.
SHIPPING:
We can ship USPS, or air freight (FedEx, UPS, DHL, or other carrier). For most air freight, we will need your tax ID number, VAT number or FedEx account number so that duties are charged to the buyer for import duties. Large equipment is shipped via crate, or shipping container.
Export HS Codes:
HS Code: 840619 Steam and other vapor turbines ex marine propulsion
Reference Document:
http://www.usitc.gov/publications/docs/tata/hts/bychapter/1002c84.pdf
CE Certification: Please inquire at time of order.
Our specialty is distributed energy and developing power systems for business that have unique power opportunities by utilizing waste heat.
Please let me know if you have any additional questions.
Secure Supplies
Daniel Mb + 66 83 647 3443
If you have a engine generator set and want to use the waste heat in our ORC equipment, you can use the coolant liquid directly, however you must convert the exhaust heat into a thermal liquid. To do this you will need a heat recovery unit. There are very efficient (up to 95 percent) units from the following:
Bowman Heat Exchangers: http://www.ejbowman.co.uk/
Airec Heat Exchangers:
Sven Persson <sven@airec.se>
Website: http://www.airec.se/
For example: QSK60-G4 Cummins QSK60 Series Diesel Generator Set 1600KW/1875KVA (1875KVA-2250KVA)
Heat Rejection to Coolant: 850 kWm x 3412 kWm/btu / (30,000 btu/kWe) = 97 kWe available CHP ORC power production
Heat Rejection to Exhaust: 1,180 kWm x 3412 kWm/btu / (30,000 btu/kWe) x 95 percent efficiency = 127 kWe available CHPORC power production
Total Waste Heat to Power ORC Production: 224 kWe
Heat Exchanger from Airec: AirCompact 70 - 160/C
Price Each For Heat Exchanger: Euro 4,500 Ex-works (shipping not included) Sweden.
INDUSTRIAL HEAT EXCHANGERS:
DCI Heat: http://www.dciheat.com
Bill Carson -CHIEF ENGINEER
Email: Bill Carson <bcarson@dciheat.com>
TEL (425) 235-1723 x101
Alfa Laval: http://www.alfalaval.com/
Luvata: http://www.luvata.com/Products/Heat-Transfer-Solutions/Industrial-Heat-Exchangers/
Ludell Mfg: http://www.ludellmanufacturing.com/product.html
Cain: http://www.cainind.com/
Diesel and Gas Cogeneration, Boiler Exhaust. For engines, retrofitting any engine or turbine, large or small, regarding combustion exhaust economizers, exhaust gas heat recovery silencers, and waste heat packaged steam generators. For boilers, rectangular or cylindrical designed exhaust economizers, recovering exhaust heat from: atmospheric boilers, Scotch marine boilers, water tube boilers, any boiler size, any fuel type, any pressure.
Contact: Cain Industries
P.O. Box 189, W194 N11826 McCormick Drive, Germantown, Wisconsin 53022 USA
Phone: (262) 251-0051 Toll Free in USA: 1 800 558-8690
Fax: (262) 251-0118
Sales: sales@cainind.com
Engineering: engineering@cainind.com
Purchasing: purchasing@cainind.com
http://www.infinityturbine.com/email/CainBoilerEconomizersBrochure.pdf
http://www.infinityturbine.com/email/CogenHeatRecoveryBrochure90180.pdf
Heatric: http://www.heatric.com/
Xyleminc: http://www.xyleminc.com/
GEA: http://www.gea-heatexchangers.com
Magen: http://www.magen-ecoenergy.com
Apischmidt: http://www.apischmidt-bretten.de
CMM Group: http://www.thecmmgroup.com/energy-recovery-systems/
REFRIGERANT - WORKING FLUID: Honeywell R245fa - Please contact Honeywell directly
https://www.rsd.net/fx/pdf/suite/honeywell_genetron/Genetron_All_Products_Spec_Sheet.pdf
Price List:
Please email us for current Price List.
Below is a basic summary of systems. Some systems may be on special - please refer to the Price List for any special discount prices that are currently offered.
Standard Pricing
System Output Heat Input Price
CHPROT06 1-3 kW Turbine/Generator Only $6,000 USD
CHPROT12 (IT10) 10 kW Turbine/DC-Generator Only: $18,000 USD
CHPIT10 10 kW 20-30 gallons/min $58,000 USD
CHPIT50 50 kW 140 gallons/min $148,000 USD
CHPIT250 250 kW 500 gallons/min $550,000 USD
CHPIT500 500 kW 1,000 gpm $1,100,000 USD
CHPIT1000 1 MW 1,625 gpm $2,200,000 USD
CHPIT2000 2 MW 5,000 gpm $3,300,000 USD
Special Note: For all models of CHPIT50-IT2MW you will need a grid-tie interconnection device, if you order with a induction AC generator. The grid-tie integrates the AC Induction motor/generator into the grid, whether it be a local (in-house) or public grid connection. This device also interacts with the PLC for proper turbine/generator operation. We also offer a IT10 in a DC PMA format that you can use with an inverter, or 12 kW AC format, which also will require the grid-tie device. The smaller the induction generator, the smaller the grid-tie device.
Biomass and Waste to Energy Systems -
We Can Reffer you to Dealers suitable to make the
Tanks of industrial quality.
GENERAL POWER CALCULATIONS (Using R134a and R245fa as working fluid)
How do I figure out the amount of power I can generate from my waste heat ?
Take your waste heat, in the form of Btu/hr and divide by 40,000 Btu (this is a general figure and can range from 30,000 btu to 50,000 btu).
For example: Total waste heat 3,000,000 Btu / 40,000 Btu = 75 kWe / hr
Note: 3,000,000 btu (3,412 btu/kWt) = 879 kWthermal
If I have a hot liquid flow of around (100 C) 212 F, how do I calculate the amount of power I can generate ? Take your hot liquid flow rate in gpm, and divide by 2-3.
For example: Total waste heat (568 L) 150 gpm / 2 or 3 = 50 to 75 kW/hr
Why are the examples not totally exact ? There are a great number of factors including type of refrigerant used, the temperature of the condenser flow water, etc.
So we prefer you work with a range of possible output.
We offer a fee based Engineering Program if you want a gauranteed performance. Larger turbine systems are easier to model and predict. Smaller turbine systems are more difficult to model.
SAVINGS in Easier Numbers
if you operate diesel generators or any of the engines below 24/7.
You may be able to capture the waste heat to generate addional kilowatts of electricity.I addion, you may reduce or eliminate the HP required to drive youradiator collant fans whether indoors or external fitments.
Exhaust to power.
With Additional wate heat to thermal oil heat exchanger, you can capture the diesel exhuast fromthe pipe to supply heat to the Turbine CHP we Supply you. The provides aprox 40% of total fuel savings as shown in chart below.
For a 100 kilowatt Prime power Diesel or Hydrogen fueled Generator, this is about8KWe per hour addional power.
Collant to PowerPipe
Staight to the CHP Turbine.This is about 32 percent of Total fuel savings as show in chart below.For a 100 Kilowatt Prime power Diesel or Hydrogen fueled Generator, this is about7 KWe per hour addional power.
Addional Radiator Fans Savings of 5% gain of HP

Waste Heat and Geothermal Power Generation
Applications
CHP ORC
Gas Turbine Waste Heat
Oil and Gas Well Heat Recovery
Organic Rankine Cycle
Rankine Cycle
microturbine
flare gas
waste heat power
waste heat
geothermal
Lumber dry kilns
geopressurized
hydrothermal
enhanced geothermal
reinjected water
Absorption Chillers
Adsorption Chillers
Automated Demand Response
Bloom Energy - The Bloom Box and other fuel cell technologies produce waste heat which can be used by the CHP Turbine to produce additional electricity
Biodiesel Refineries
Biofuel Refineries
Biomass Gasification
Cogeneration
Concentrating Solar Power
Demand Response Programs
Demand Side Management
Engine Driven Chillers
Solar CHP
Solar Cogeneration
Solar Heating and Cooling
Solar Trigeneration
Trigeneration
Cement Plants
Refineries
Dry Kilns
Production of ice
Fresh Water Desalination
Other General Applications
•Distributed power generation
•Onsite generation at point of use
•Military power systems
•Transportation propulsion systems
•High energy-consumption sites
•High energy-cost markets
•Facility base-load power
•Peak shaving
•Sites isolated from grid power
•Utility substation generation
•Combined heat and power (CHP)
•Environmental and energy service company (EESCO) installations
HEAT RATE AND EFFICIENCY
Note: If you have to pay for your heat or fuel, the CHP ORC process does not make any financial sense to install.
CHP ORC is a bottoming cycle, and designed for waste heat (free heat). As for supercritical CO2 Brayton Cycle, it is about the same or lower efficiency as
CHP ORC at or below 200 C. Above 500 C The S CO2 cycle will start to have efficiencies from 40+ percent. This process needs funding to be fully developed.
Heat Rate: In general waste heat is recovered via thermal oil, water or glycol solution.
Our CHP ORC systems can use heat in the range of 80-140 C input heat. If it is lower than 100 deg C, then figure on 40,000 BTU / kWe. The heat rate is better as input heat temperature goes up and condenser cooling water goes down. The smaller a system (1-10 kw) the heat rate is even higher.
Our standard system is the R 245fa (Honeywell Genetron) system which operates between 80-140 C within our parameters. This represents 8-11 percent efficiency. R245fa has proven to be the most efficient refrigerant in this heat range.
Input Fluid: Using water, glycol or thermal oil (for higher temps) you can expect a flow rate of 2-3 gpm (7.6 to 11.4 liters/min) per rated kW. So a 60 kW rated system needs around 150 gpm. Expect a temperature drop of 15-20 C between the input and exit of the evaporator.
Condenser: The standard systems use a water cooled condenser.
Expect a temperature increase of 5-10 C from the input and exit water flow. There are a few novel condenser designs which will allow a greater cooling rate, and lower water flow rate.
These include ejector cooling, Zeolite pellet condenser design, and using our new counterflow turbopump, which uses the turbine power to spin a turbopump that cools the exiting gas from the turbine as a pre-heater.
There are also nano-fluid additives which may increase heat transfer efficiency.
GENERAL ORC INFORMATION
Our Organic Rankine Cycle (CHP ORC) Infinity Turbines can use any thermal fluid to power the system evaporator (which in turn evaporates the high molecular mass fluid - an environmentally friendly refrigerant). As for your waste heat, we recommend you run that through a heat exchanger that has thermal oil as the fluid, which we can then run into our system.
How it works: The organic Rankine cycle has three steps -
(a) Your heat is provided in the form of thermal liquid (water, glycol or oil). If you already have heat exchanger equipment, then you can just use water, glycol, or a better alternative is thermal oil.
If you don't have a heat exchanger to capture your waste heat, then we recommend a hot air to thermal oil exchanger (they are available everywhere). The source of the heat can be geothermal, engine waste heat, gas turbine heat, solar collector, industrial waste heat, steam, etc. Your heat source in the form of a liquid then goes through the evaporator heat exchanger.
This is where the working fluid for the CHP ORC turbine gets vaporized and pressurized. The heat source should be at least 80 deg C. Once it passes through the evaporator, it comes out at about 10-15 deg C cooler. This can then be used for additional process heat (CHP hot water or chiller).
(b) The working fluid for the CHP ORC closed system is pressurized by the evaporator, then is expanded by our turbogenerator. This produces the shaft horsepower to turn the generator and produce electricity. Of course, you can have the turbine power a generator, pump, or whatever you require.
(c) The expanded working fluid then goes through a condenser to return the vapor to a liquid state. The condenser requires some method of cooling fluid, typically water which is provided from a cooling tower, or ground based geothermal (the ground has a constant temperature of 15 deg C or less temperature). The liquid is then pumped back into the evaporator unit to complete the cycle. Only environmentally friendly working fluid is used in the system.
So, the basic system has a evaporator, turbogenerator unit and condenser.
The temperature difference between the evaporator and condenser heat and cooling flows must be at least 125 deg F, or about 65 deg C (difference).
Our heat rate is about 40,000 BTU / kilowatt electricity which is about 5-11 percent efficient. This system is geared towards waste heat - so it's free power.
It's possible to use steam or steam condensed (condensate) hot water to put into the evaporator (boiler) to run the system if that is available on site.
ORDER NOTES AND TERMS
Prices are in US Dollars unless otherwise indicated and are subject to change. When you are ready to order, please request a formal invoice and wire instructions. We do not accept Letters of Credit.
Order Terms For Large Orders Above $50,000 USD: 40-60 percent down, 30-40 percent at a progress payment time period, balance at time before shipment to customer. NON-REFUNDABLE DEPOSIT:
Once an order is placed, initial deposit is non-refundable if customer cancels. EXPERIMENTAL: Unless otherwise noted, all our CHP ORC systems, components and parts, are experimental.
Order Time: From time of deposit on equipment the mfg. time is around 4-6 months depending on orders in process. For custom builds, this time will vary. All build time may vary according to supplier delays, which we have no control over.
To run completed unit, you will need to provide hot fluid (water, oil, etc.) to run through the evaporator heat exchanger. You will also need condenser cold fluid, which may be provided by an air cooling tower, ground source geothermal, or cold water from another source.
These units come without working fluid (refrigerant). The buyer will need to purchase refrigerant and install the refrigerant at time of equipment installation.
BIOMASS ENERGY - WOOD ENERGY:
Our biomass systems are custom built.
To quote any full biomass system, we will have to do an Engineering Study (fee based).
In general, our heat rate is 40,000 btu/kWe. That means that you need to input 40,000 btu/hr of energy from wood or biomass for each kilowatt of electricity produced output.
Typical biomass, depending on moisture content, will range from 4,000 btu/lb for moist and up to 8,600 btu/lb for dry biomass.
This means that there are about 17,000,000 btu per ton for dry wood waste and only about 8,000,000 btu per ton for green or moist wood waste.
So the amount of wood waste needed to fire a biomass boiler, will depending primarily on the moisture content.
While you can use a variety of wood boilers, we recommend a batch fed, top fed system which eliminates the fuel (wood waste) handling.
In general, if you have to pay for the fuel source (wood waste), then these types of installations don't make any financial sense, since ORC is really designed for waste heat and only 6-10 percent cycle efficiency.
The benefit of a CHPORC system is that you do not need a full time attendant, like you do with a steam system.
This is a code currently in the USA for steam systems above 15 psi pressure.
WHATS IN THE KITS
KIT A.
STANDARD ORC TURBINES AND SYSTEMS FROM INFINITY TURBINE CURRENTLY IN PRODUCTION:
CHPIT10 (RIT - Radial Inflow Turbine) (single module) Turbine Only - Magnetic Coupling - 2015 Version:
-
Turbine Mag Coupling: Please see our current pricing.
-
Power: Can drive a generator up to 10,000 watts DC power out. May have higher output with increased rpm and flow rate.
-
Inlet Port: 1 inch Can drive up to 10 kW Generator
-
Outlet Port: 4 inch flange or NPT
-
Working Fluid: R134a, R245fa, compressed air.
-
We have not tried other pressurized gases or fluids. When using any working fluid, you need to have a lubricant in the pressuized flow to lubricate the bearings.
-
Pressure: 50-200 psi working pressure (up to 20 bar, 2 Mpa, 2,000 Kpa tested). We have not tried higher pressures in operation.
-
RPM's: 3,000-20,000
-
Material of Turbine Assembly: 304 stainless steel turbine and aluminum assembly. High speed bearings.
-
Mounting Bolts: Mounting bores on bottom of unit. Size 3/8 threaded bore.
-
Seals: Unit is hermetically sealed. Entire unit sealed. Two sizes of o-rings.
-
Availability: 4-6 weeks estimated.
-
Measurements: See price sheet.
-
Weight: See price sheet.
-
Shipping: Optional via air freight, surface or priority international air.
-
Type: Not CE Certified. Experimental.
-
Generator Options: Since this is a magnetic coupling, there is a receiver mag rotor which has a 17 mm shaft bore, that allows you to attach the mag rotor directly to your generator. As an option, you can source a copper coil to put on the back block (outside) which uses the spinning interior mag rotor to supply the magnetic flux.
-
Shipping: (1) crate holds product of 187 lbs, dimensions are 16 X 17 X 20 inches.
Kit B
CHPIT10 ORC System.
-
Framed system includes two flat plate heat exchangers (ASME or approved), expansion tank,
-
ITxr turbine-generator (DC power output), feedpump. System is fully piped and pressure tested.
-
Ships without refrigerant. Manually controlled. Experimental.
-
Dimensions and weight: Please see price list.
-
Crating charge: Please see price list. Shipping not included.
-
Approximate mfg. time is 6 weeks.
-
Pricing: Please see our current pricing.
-
Dimensions are 60 1/2" (1550 mm) L x 30 1/2" (788 mm) W 68 1/2" (1753 mm) H finished crate. Heat treated and certified crate is 7/16 OSB.
-
Shipping Weight: 930 lb and 2.24 CBM
Scope of supply
The heat recovery generator set is a skid mounted non-enclosed assembly consisting of a flat plate evaporator, a flat plate condenser, a turbine PMA DC generator assembly, a working fluid circulation pump and a refrigerant holding tank, all frame mounted. The turbine/generator assembly consists of a single element turbine connected to a PMA DC generator.
This heat recovery generator set converts moderate temperature liquid heat sources to electricity through the vaporization and expansion of a working fluid in a closed system. The working fluids (not included in purchase price) to be used in this piece of equipment include
R134a and R245fa.
Description
Framed system includes two flat plate heat exchangers (ASME approved), expansion tank, ITxr turbine-generator (DC power output), feedpump. System is fully piped and pressure tested. Ships without refrigerant. Manually controlled. Shipping: Weight: 680 lbs of product, 930 lbs gross (422 kg). Dimensions are 60 1/2" (1550 mm) L x 30 1/2" (788 mm) W 68 1/2" (1753 mm) H finished crate. Heat treated and certified crate is 7/16 OSB.
End User Supplied
Secue Supplies strongly recommends that the end user include an automatic shut off valve and/or a by-pass loop in the piping of the inlet and outlet of the evaporator. Protective relays and sensors that may be required by a local utility are the responsibility of the end user.
Disclaimer: Secure Supplies is not responsible for confirming the suitability of this proposed generator set for any specific application or any specific jurisdiction. Individual design elements may be changed without notice or prior consent as long as the overall performance of the end product is not adversely effected. END OF SCOPE OF SUPPLY
KIT B.
CHPIT50 Series Frame Mounted Waste Heat to Energy Platform:
50 kW Net Output
-
CHPIT50 CHP ORC System (with shell and tube heat exchangers):
-
System Availability: 12+ weeks.
-
Complete CHPIT50 ORC System: Please see our current Price List.
-
Generator to Inverter Output: 60 kw gross output, 50 kw system net output power.
-
Description: CHP ORC system for engine waste heat, biomass, or hot springs geothermal. Inflow Radial turbine generators.
-
Designed for CHP ORC refrigerant working fluid. Design working pressure 150-200 psi.
-
Heat Exchanger Ports: 2 inch Female NPT inlet and outlet.
-
Initial Fill and Extra Refrigerant: 600 lbs. This is not included in any system, and must be provided by the buyer.
-
Electrical - NEMA 3R Oiling System - Gearbox only, Splash fed Protective Relays - Field supplied by others Noise - Less than 80 dBA at 10 metres (32 feet)
-
Shipping Information:
-
Overall Dimensions: 108 in (9 ft) x 55 in (5 ft) x 76 in (6 ft), 6700 lbs.
-
Made in USA. HS Code: 840619 Steam and other vapor turbines ex marine propulsion 8406.90.7500 Parts of other vapor turbines.
-
Evaporator/Condenser - Two pass, ASME Section VIII compliant. (ASME stamped)
-
- Heat Transfer Capability: from 2.1 million btus/hour [at 203 degrees F (95 C) and heat source flow of 5 feet per second] to 3.5 million btus/hr
-
- Tubes: finned copper .750 inch outside diameter, heat transfer rate minimum 1317 btu/hr/deg F/ft2 , Wolverine Tube design Turbo BIII or similar.
-
- Shell: carbon steel seamless tubing, over all length 72.0 inches, outside diameter 10 inches, wall thickness .375 inch
-
- Insulation: one inch semi rigid with an aluminum wrap. Insulation includes the evaporator to turbine manifold.
-
- Typical requirement of liquid waste heat source 120 to 150 US gpm.
-
Gearbox:
-
None. Direct drive AC generator.
Generator: The generator is a induction or synchronous A.C. three phase unit with integral regulator to provide continuous output as follows: 60 Hz, 460 - 600 volt, .8 PF, 3,600 rpm, full load output 69 kWe minimum. Europe Version: 50 hz.
KIT D
CHPIT100 ORC:
TBA
KIT E
CHPIT250 Series ORC
Model IT250 is an Organic Rankine Cycle (ORC) engined generator set that has a net electricity output of 250 kWe when operating at full load under design conditions. Model IT250 operates on energy provided by a variety of moderate temperature liquid heat sources including process heat that would otherwise be released into the environment (so called waste heat) and renewables such as geothermal or solar trough outputs.
-
Generator Type - Synchronous or Induction, 3,600 rpm nominal for 60 hz, 3,050 rpm for 50 hz.
-
Net Electricity Output - up to 250 kW* Voltage - 380-420 volt AC, 3 phase (230 volt option) Frequency - 50 / 60 cycle
-
Power Factor - .9 lagging Heat Source - Water/glycol or equivalent, 90 degrees to 140 degrees C.. Cooling Source - water 5 to 27 degree C.
-
Operation - Guarded plant or unattended Controls - PLC based, to suit end user. Remote monitoring optional - available Plumbing -
-
ASME standard Heat Exchangers - ASME Section VIII , Two pass Shell Side Pressure Rating - Evaporator, 400 psig -
-
Condenser, 150 psig Electrical - Noise - Less than 80 dBA at 10 metres (32 feet) Overall length - 16 ft 10 inch Overall width - 7 ft 8 inch
-
Overall Height - 8 ft 8 inch operational, 7 ft 6 inch for shipping
-
Dry Weight - 21,000 lbs
-
Gross Power Out..........283 kWe
-
Net Power Out.............250 kWe
-
Working Fluid (245fa) Charge .............3,200 lbs
-
Heat Source Supply (water/glycol) minimum.................340-500 US gpm
Kit F
CHPIT2MW
-
The price is $3,000,000 USD.
-
Expect a build time of 6-12 months, with current customer orders.
-
The generator is rated for 2,500 kW gross power output, 2,000-2,200 kW net power output.
-
The footprint of the ORC system would be as follows:
-
1 x 40 ft. container with the evaporator
-
1 x 40 ft. container with the condenser and feed pump
-
1 x 20 ft. container with turbine, generator and PLC system
-
The modules would be connected on site for rapid deployment.
-
Shipping costs about $30,000 USD to any major port or city in the world, for the entire system.
![]() 1.png | ![]() Chp Control box Combined Heat power.png |
---|---|
![]() Chp Controller Software.png | ![]() geo thermal hydrogen fittings.png |
![]() engine chp china generator.png | ![]() CHP1.png |
![]() Chp Turbine.png | ![]() CHP thermal heat.png |
![]() Geo thermal Turbine.png | ![]() CHp Software Systems.png |
![]() Geothermal CHP Turbine.png | ![]() CHp Power systems.png |
![]() CHP Geo thermal Hydrogen.png | ![]() Chp Engines Machines Production line.png |
![]() Chp Factory.png | ![]() Chp Fittings engine power best.png |
![]() Chp Fittings.png | ![]() chp engine factory australia.png |
![]() Chp engine fittings.png | ![]() Chp Engine heat power China.png |
![]() CHp Engine Plumbing.png | ![]() CHP Engine Europe Heat Power Thermal recovery.png |
![]() CHp Engine Controllers.png | ![]() Chp Engine Controller software.png |
![]() Chp Engine Combined heat power China.png | ![]() CHP Engine China USA Australia Europe BEST Leading First33 .png |
![]() Chp Engine Software Controllers.png | ![]() CHP Engine China USA Australia Europe BEST Leading First1 .png |
![]() CHp Controller Technology.png | ![]() CHP Engine China USA Australia Europe BEST Leading First.png |
![]() CHP Engine China USA Australia Europe BEST Leading First 22 .png | ![]() CHP Engine China USA Australia Europe BEST Leading First 11 .png |
![]() CHp Engien Factory.png | ![]() Geothermal Factory Hydrogen.png |
![]() Geothermal Hydrogen.png | ![]() geothermal Turbine.png |
![]() geothermal Turbine112png.png | ![]() High Quality CHP Turbine.png |
![]() installing turbine engine 22.png | ![]() installing chp turbine engine.png |
![]() installing chp turbine engine 333.png | ![]() Japanese Chp engines 1.png |
![]() japanese chp engines.png | ![]() Hydrogen CHP.png |
![]() installing chp turbine engine 1.png | ![]() installing chp turbine engine.png |
![]() installing chp turbine engine 1.png | ![]() Power Untis controllers Chp Engines.png |
![]() Turbine air in.png | ![]() Turbine CHP Geo Themal ff.png |
![]() Turbine CHP Geo Themal.png | ![]() Turbine Facotry.png |
![]() Turbine Factory power.png | ![]() turbine factory.png |
![]() CHP Engine Hydrogen power plant.png | ![]() Awesome Turbine chp.png |
![]() Beautiful Turbine.png | ![]() chp engine homes.png |
![]() CHP Engine Turbine Blades housing design manufacture.png | ![]() CHP Engine Hydrogen.png |
![]() CHP Engine Hydrogen power.png | ![]() World best Chp Turbine.png |
![]() Worlds Best CHP Engine.png | ![]() Worlds Best CHP.png |
![]() Turbine Chp Engine heat power.png | ![]() Small CHP Engine.png |
![]() KW CHP Turbine Sizes.png | ![]() machine thermal heat to power.png |
![]() Micro Power from Heat.png | ![]() Micro Turbine CHP Heat power.png |
![]() Sexy turbine.png | ![]() Heat Stack Power.png |
![]() Heat Recovery Power CHP.png | ![]() factory heat to power.png |
![]() Engine Kits .png | ![]() Compressor CHP Turbine.png |
![]() Combined Heat and Power Machine.png | ![]() Combined Heat and Power plant.png |
![]() Combined Heat and Power steam.png | ![]() Combined Heat and Power Top of range.png |
![]() Combined Heat and Power.png | ![]() Combined Heat and Power home .png |
![]() chp.png | ![]() CHP Turbine Technology.png |
![]() Chp Turbine rotor baldes.png | ![]() CHP Turbine Hydrogen on demand.png |
![]() CHP Housing.png | ![]() CHP Steam Turbine.png |
![]() CHP Super Charged Delux Trubine Engine.png | ![]() CHP turbine Engine Hydrogen power plant 1.png |
![]() CHP turbine Engine Hydrogen power plant.png | ![]() CHP Fittings.png |
![]() CHP Engine Hydrogen power plant 2.png | ![]() Wrodls Best Chp Combined heat power.png |
![]() Tubine For Sale.jpg | ![]() CHP Generator Kit Power Plants 1 .png |
![]() CHP Generator Kit Power Plants.png | ![]() CHP Tuirbine.jpg |
![]() CHP UNITS.jpg | ![]() 3.png |
![]() 4.png | ![]() 5.png |
![]() 6.png | ![]() 7.png |
![]() 2.png | ![]() 1.png |
![]() 8.png | ![]() 11.png |
![]() Untitled.png |
-
look up ground heat thermal maps,
-
go deep 1000 m or more, use steep copper loops
-
make steam or use other redridgerants
Call
T USA : +1 520 906 2455
T TH : + 66 (0)86 647 3443
© 2009 SECURE SUPPLIES LIMTIED by Daniel Donatelli All Rights Reserved. No duplication is permitted of this site graphically or conceptually unless requested and approved in writing.
All Rights Reserved Worldwide. Copyright © 2012 Secure Supplies Limited Daniel Donatelli © 2009
Copyright Disclaimer Under Section 107 of the Copyright Act 1976, allowance is made for -fair use- for purposes such as criticism, comment, news reporting, teaching, scholarship, and research. Fair use is a use permitted by copyright statute that might otherwise be infringing. Non-profit, educational or personal use tips the balance in favor of fair use.
Please help make the change to clean fuels It is time to order.
Share it First