Secure Supplies
Energy Power Gas Magazine
Fueling Healthy Communities
Secure Supplies
Energy Power Gas Magazine
Fueling Healthy Communities
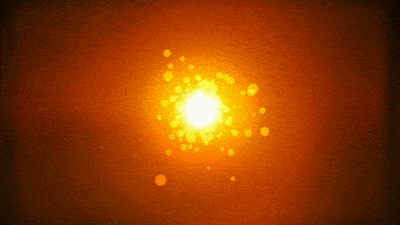
Secure Supplies Group
Montana
Power Gas Energy News
Access Key policy Events and key Project updates
for Montana's economy.
CHS adds hydrogen plant for improved fuel production
What does it take to understand why CHS built a new hydrogen plant at its Laurel refinery? How about grasping how it works and what it’s purpose is? A degree in engineering, as it turns out.

Recently three of the top supervisory engineers at the CHS Refinery in Laurel did a good job of explaining the purpose of the plant on the south side of the refinery’s property and why the company built it, but the complexities of its inner workings are best left to them.
“Basically, hydrogen is made out of natural gas,” explained Brandon Gauthier, the project manager. “It’s created from a mixture of natural gas, steam and heat.”
The Laurel refinery already had two smaller hydrogen plants, according to Dan Wohlgenant, refinery operations manager. The new plant—the culmination of two years of work—adds an additional 40 million cubic feet of hydrogen per day to the refinery’s capacity.
According to Ben Mossman, operation superintendent, the hydrogen isn’t an end product.
“We use it to remove sulfur and nitrogen from fuels,” he said. “Im
agine the long chain of hydrocarbon. It is split and turned into shorter molecules.”
Wohlgenant clarified, “We take lower value oils and turn them into diesel and gasoline.”
Besides two years of planning, it took 250 contractors on site and about $100 million to build the plant. While the construction phase is complete, testing of the equipment is only about halfway done.
“We’re in the process of going online,” Mossman said. “We’re working piece by piece through the plant to ensure everything is functioning.”
All three men agree that the addition of the plant was a big project for CHS, at least for the Laurel location. And, anyone who witnessed Laurel’s First Avenue being cleared of traffic—even the power lines were lifted—for the transit of two large tanks down the street from Buffalo Trail can attest to the size of some of the plant’s components.
“Overall, our facility is about the same size as the others in the valley,” Wohlgenant said. There are about 300 full-time employees working at the refinery, he said. Two hundred of them are union members.
“The refinery provides a lot of good jobs and the work allows a lot of people to stay in the state,” Gauthier noted.
As the building manager, Gauthier oversaw the engineering and design of the plant, procurement of the necessary components and the construction. Mossman ensures the plant stays within the environmental permit limits, that personnel follows safety protocol and that the plant operation is reliable and efficient. Wohlgenant oversees operations for the entire refinery.
“The hydrogen plant is built with the latest technology for pollution control,” Gauthier said. “Technip was the builder and they use the best and most innovative designs.” Among the local contractors were Weldtech, COP, and APEX, he said. Each of those companies, in turn, provided employment for many local workers.
Although operators can work at the hydrogen plant or at other areas of the refinery, most of the actual running of the plant is done remotely, in a control room via computer. It took a large workforce to get the new plant built, but overall CHS only increased the number of regular operators by four.
“But we doubled our hydrogen capacity,” Gauthier. According to Technip’s website, “hydrogen is the most widely used industrial gas in the refining, chemical and petrochemical industries.”
Do you know more about this story? Contact us through this link.
Click here to learn about advertising, content sponsorship, events & round tables, custom media solutions, whitepaper writing, sales leads or eDM opportunities with us.
To get a media kit and information on advertising or sponsoring click here.
PROUD TO BE ASSOCIATED ACROSS OREGON WITH
