Secure Supply Kenya
Fueling Healthy Communities
Power Gas Architecture | Developer
Secure Supplies Group
Mr Derrick James Kimani,
Nairobi , Kenya +254 721 661501

Hydrogen Fueled Ovens and Stoves
One of our most Popular Products send all over the world
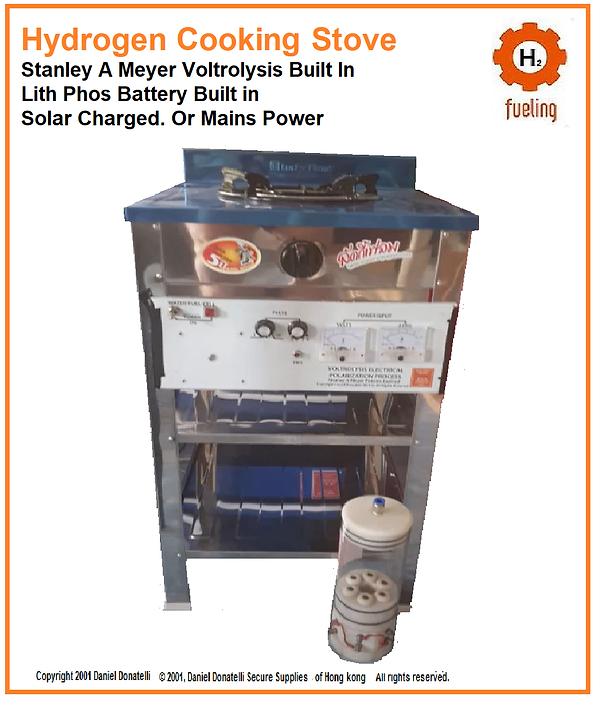
For many people their FIRST hydrogen appliance is a stove!
Many people get these inexpensive burners to familiarize themselves
with hydrogen gas. Great for boiling water and cooking meals AND HEATING YOUR HOME!
YES! Heating your home! Remember burning Hydrogen gas does NOT produce carbon monoxide fumes, only water vapor is produced keeping your home warm and moist in thus cold winter months just ahead.
Finally get ride of thus high winter fuel bills and humidifiers.
100% efficient heating is here now in the Hydrogen Age!
Those of you who would like to Order our Stoves
We are in the first stages of distribution and would like only order of 12 pcs up
We can supply by container also aprox 1000 pcs per 20 fcl shipping container
We have Stove top units , burners for conversions
and tips for oven conversions etc
Daniel Donatelli
Mb + 1 520 848 1659
Hydrogen Stove Total 599.50

Fuel on Demand Kit
This Kit will run from solar or battery bank to make your Gas to replace lpg etc
The Cell 12 volt Version
for 12 volt solar to gas battery to gas or mains to gas
12v 20 plate Oxy/Hydrogen generator
US $320.00 In Stock .
Oxy/Hydrogen is 66% hydrogen and 33% oxygen. It is produced as a mixed gas.
It is also called HHO and Browns gas.
This cell is designed for use with a 12 volt power source.
Featuring
.1 to 2.0 liters per minute of Oxy/Hydrogen production.
316 laser cut Plates.
High temp. dye cut EPDM rubber gaskets.
3/4 superior high temp. HDPE end caps.
Automatic cooling system built right into every cell.
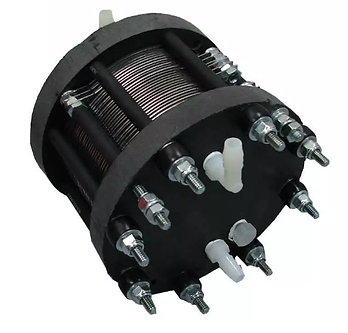

PWM plus 12V/40Amps
Full Computerized with 2MPUs
3 sensors BPS, CCS, ECS, CGPS, Wi-fi
WIF Enabled PWM Controller 12 v US $279.50
Cooking Gas Cell US $320.00
Gas Production Kit Total 599.50
Shipping $60
The Cell 24 volt Version
for 24 volt solar to gas battery to gas or mains to gas
34v 20 plate Oxy/Hydrogen generator
US $320.00 In Stock .
Oxy/Hydrogen is 66% hydrogen and 33% oxygen. It is produced as a mixed gas.
It is also called HHO and Browns gas.
This cell is designed for use with a 24 volt power source.
Featuring
.1 to 2.0 liters per minute of Oxy/Hydrogen production.
316 laser cut Plates.
High temp. dye cut EPDM rubber gaskets.
3/4 superior high temp. HDPE end caps.
Automatic cooling system built right into every cell.
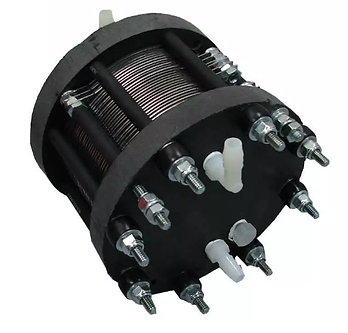

PWM plus 24V/40Amps
Full Computerized with 2MPUs
3 sensors BPS, CCS, ECS, CGPS, Wi-fi
WIF Enabled PWM Controller 24 v US $279.50
Cooking Gas Cell US $329.50
Gas Production Kit
Total 609.00
Shipping $60
BIG PUPPA
Solar + USB Battery + Charge Controller Kit
This Unit will Charge from Sun or from Mains Power
It will connect to your Gas Maker and Hydrogen Stove
-
Solar Panel
-
Charge Controller
-
Lithium Battery
-
Invertor
-
USD Port for Device powering like LED LIghts, Phones Battery Banks
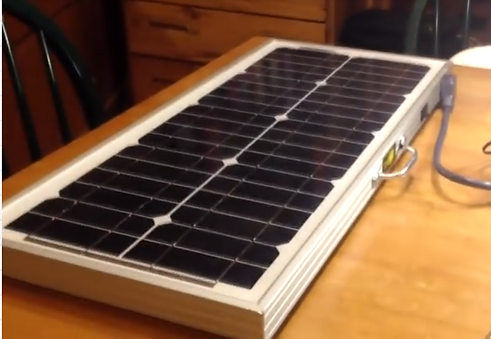




4 cell configuration: Stock – For smaller loads. Approximately a 120 watt hour battery.
8 cell configuration: $320 – For larger loads. Approximately a 240 watt hour battery.
Little Mumma
Solar + USB Battery + Charge Controller Kit
This Unit will Charge from Sun or from Mains Power
It will connect to your Gas Maker and Hydrogen Stove
-
Solar Panel
-
Charge Controller
-
Lithium Battery
-
USD Port for Device powering like LED LIghts Phones
-
2 x Light Lights

Industrial on site gas
Industrial Pizza ovens Dryers Kitchen that use Gas Etc
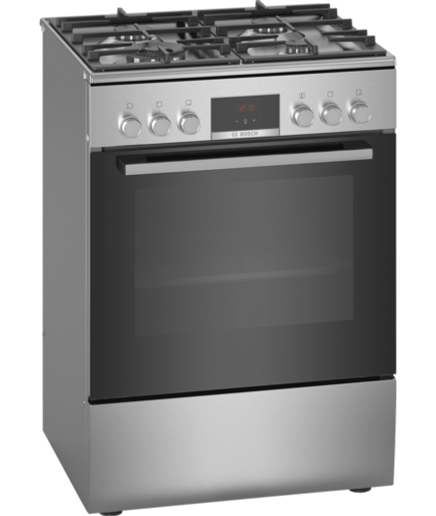


New Model for 2020
Ultra-low NOx emissions from catalytic hydrogen combustion

Complete hydrogen stove setup " gas under glass " , hydrogen flow 6.6 Nl/min, air flow 33.5 Nl/min, SiC burner temperature 922°C.

Infrared image of the SiC burner at operating temperature.

SELF energy cycle: solar radiation is converted to electrical energy and stored in batteries, surplus energy is used to produce hydrogen, stored in metal hydrides.

Catalytic diffusive hydrogen burner set-up, H 2 supply from below, air supply from the top.
Development of a catalytic hydrogen burner
A novel self-igniting catalytic hydrogen diffusion burner has been developed, based on reticulated porous SiC ceramics [2], coated with platinum as highly active catalyst [3]. Compared to converting hydrogen into electricity by a fuel cell and using an electric stove for cooking, the direct conversion of hydrogen into heat shows much higher conversion efficiency while reducing safety issues through system simplicity [1].
The high passive safety measure is reached by separately feeding hydrogen from the bottom and air from the top of the porous catalytic active SiC ceramics (Fig. 3). The gases then mix directly on the Pt coated highly porous silicon carbide surface, where the hydrogen is immediately oxidized by the redox reaction of hydrogen with oxygen from the air, activated by the Pt based catalyst [4] according to the stoichiometric reaction:
2H2 + O2 Æ 2H2O
This exothermal reaction releases sufficient heat for cooking or heating purposes while emitting only water vapor as a byproduct. Due to the absence of carbon and the relatively low combustion temperature of < 1200 °C, no hazardous gases are formed.
As we have introduced a catalytic combustion approach, no ignition spark is required and no open flame is generated as common in conventional gas stoves [3, 4]. Thermal power regulation is reached simply by adjusting the supply of H2 and air.
The initial design of the hydrogen burner consists of a porous SiC hydrogen diffusor with an open cell foam of 100 ppi (pores per inch), overlaid with a porous SiC foam of 80 ppi with a porosity of ca. 87% (Lanik Foam Ceramics, CZ) (Fig. 3, 4). The upper foam is coated with platinum as catalyst. The platinum load is ca. 200 mg on a SiC foam of 150 mm diameter, 10 mm thickness and an average weight of 75 g, corresponding to 0.26 wt% of platinum load.
Hydrogen is supplied from below through a brass based pre-gasdiffusor into an expansion chamber and penetrates through the main porous diffusor to the catalytic coated porous SiC ceramics. There H2 reacts at the triple points H2-O2-Pt inside the porous SiC structure according to the equation above.
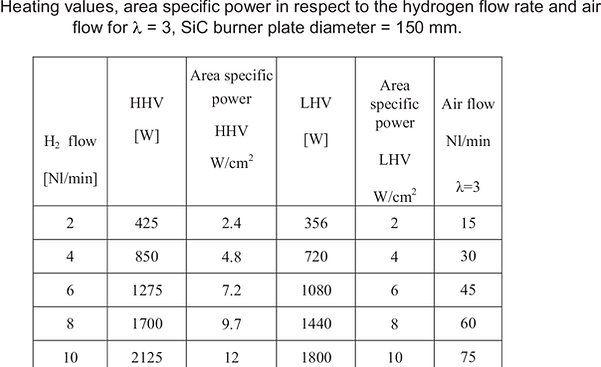
Excellent Performance

Dependence of hydrogen slip vs. hydrogen flow at different values.

Temperature on SiC ceramic (on plate) and glass ceramic (on ceramic) in relation to hydrogen flow and values.
Catalytic Hydrogen Combustion on Porous SiC Ceramics
A novel catalytic diffusion burner for hydrogen, based on highly porous silicium carbide (SiC) ceramics and platinum (Pt) as catalyst has been developed for applications like cooking stoves or room heating. By preventing gaseous hydrogen and oxygen from mixing prior to the catalytic reaction zone, a high passive safety standard is assured.
Through the self igniting property of hydrogen and oxygen in contact with platinum no ignition spark is required. Highly porous SiC foams are used in the combustion zone due to their high temperature stability and thermal shock resistance. Platinum is applied as catalyst on the SiC surface, as it has a high catalytic activity with hydrogen and oxygen even at low temperatures.
To prevent any pre-mixing of fuel and oxidant prior to the catalytic zone and thus assure a very high safety standard, hydrogen is fed from below the porous Pt coated SiC foam and air as the oxidant is supplied to the top. In this manner the oxidation process occurs only inside the Pt coated porous ceramic structure and no open flame is developed. The thermal power can easily be regulated by adjusting the hydrogen and air flow rate and thus temperatures up to 1000 °C can be reached.
The combustion of hydrogen produces no carbon oxides and below 1200 °C no nitrogen oxide is generated, the only exhaust product from the reaction is water vapour. The new developed burner system can thus be used safely indoors without any air ventilation system. In the applied cooking stove design, the gas under glass technology was introduced by using a conventional glass ceramic cover for a comfortable and convenient appliance
For cooking purposes a self igniting catalytic hydrogen diffusion burner, based on highly porous SiC ceramics with a catalytic platinum coating, has been developed for SELF. SELF is a mobile autarky living and working unit, acting as a research and demonstration platform for novel building and energy technology systems [1].
The unit furnishes users with all common living comforts, on board renewable electricity generation provides
electric power. Key challenges faced are the continuous energy and water supply. Fluctuations in the supply of electrical power and water have to be backed by on board storage, whereby seasonal fluctuations demands large storage capacities.
A photovoltaic power plant is the source of electricity, lithium ion batteries are the prime chemical electrical storage. In addition to the battery buffer, an AB5 metal hydride storage is implemented to support storage of surplus electrical energy as hydrogen for buffering seasonal energy fluctuations. A proton exchange membrane (PEM) electrolyzer is used to convert electric energy into hydrogen. Storing energy in the form of hydrogen allows a higher volumetric and gravimetric energy density in relation to battery storage. (Fig. 1) [1].
The self igniting catalytic hydrogen diffusion burner has a very high passive safety measure, based on the strict separation of hydrogen and air, as the gases are mixed only on the catalytic coated porous silicon carbide surface (Fig. 3).
Hazardous gases such as carbon monoxide, carbon dioxide, nitrogen monoxide and nitrogen dioxide are no issue. For a high cooking comfort the gas under glass technology was introduced by using a glass ceramic cover
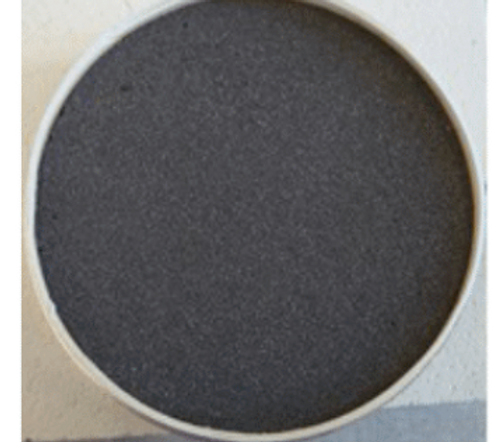
Fig. 4: Diffusive catalytic hydrogen burner made of Pt coated porous SiC.
2. Experiments and Results
The above described design prevents premixing of gaseous hydrogen and oxygen prior to the reaction zone and thus assures a very safe oxidation process. When exposed only to convectional air supply [4], the reaction area specific power ratio is limited [5].
To improve the oxidation process which in turn increases the area specific power necessary for a cooker, an advanced concept with forced air supply was developed (Fig. 5 & 6). In this design, air is pumped to the top of the ceramic burner surface through steal tubes with nozzles of 0.5 mm diameter. Air is forced in contrasting direction to convection, improving air penetration into the catalytic coated porous ceramics [6].
Thus higher air and hydrogen flows can be deployed, achieving higher overall area specific power ratios
(Table 1).
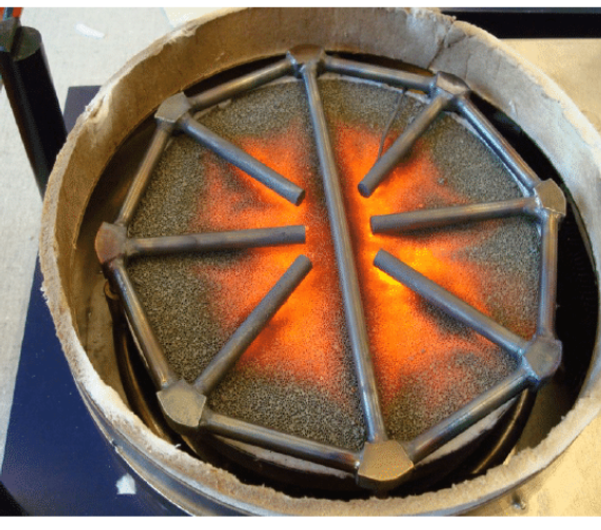


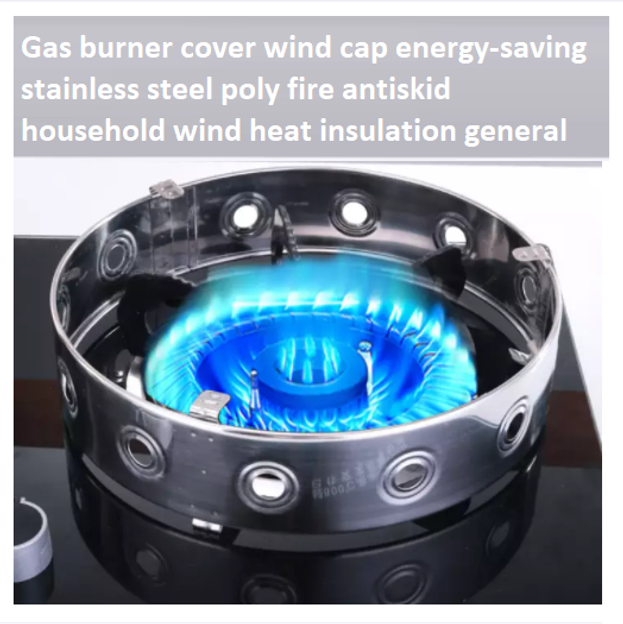
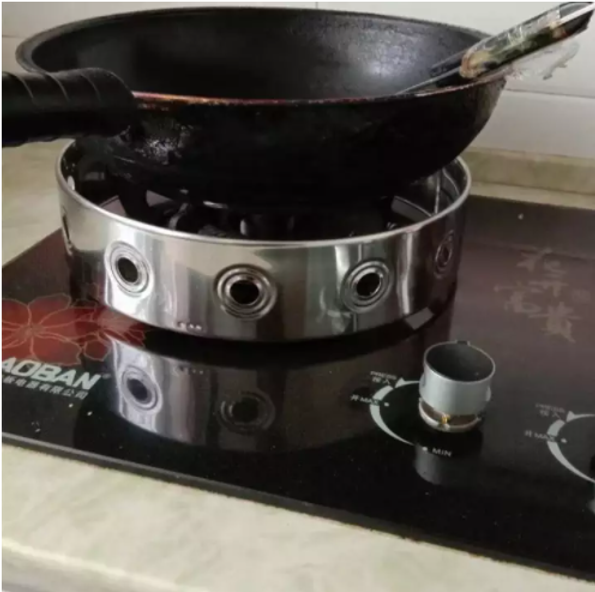
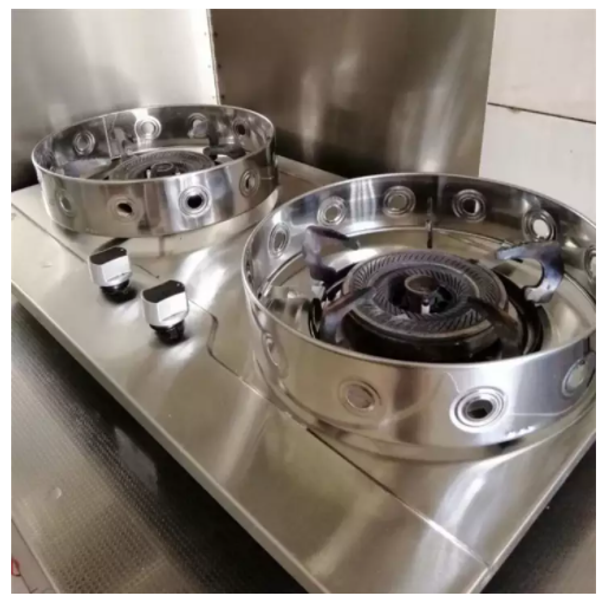



Fig. 6: Principle of the catalytic hydrogen burner with hydrogen supply from below and
forced air supply from the top.
This approach allows a controlled airflow and specific ratios of air to hydrogen can be
applied. While the stoichiometric value of 1O2: 2H2 ( =1) is the minimum ratio of oxygen to
hydrogen required for the complete oxidation reaction, in practice is between 2 and 3.
In table 1 the area specific power densities in respect to hydrogen and air flow for = 3 are
shown.
Table 1: Heating values, area specific power in respect to the hydrogen flow rate and air
flow for = 3, SiC burner plate diameter = 150 mm.
To verify a safe operation, an important issue is the hydrogen slip during operation. This
refers to the amount of hydrogen which passes the catalytic porous burner without being
oxidized. Hydrogen slip occurs mainly due to poorly distributed oxygen on the catalytic
burner plate or locally insufficient hydrogen to air ratios.
A low hydrogen slip improves
safety aspects and is an important issue concerning total efficiency [6].
For quantifying the hydrogen loss, online mass spectrometry (H-sense, V&F
Analysetechnik) was used to analyze the exhaust gases. By this analytical technique, the
mass to charge ratio of charged particles are measured.
The quantification is done in parts
per million (ppm) of hydrogen in the exhaust air. Testing was carried out to distinguish the
optimal air to hydrogen ratio in respect to hydrogen slip and SiC burner temperature as
well as glass ceramic surface temperature. Hydrogen flows of 2 Nl/min to 8 Nl/min were
tested with values of 1.5 to 3, as shown in figure 7 & 8. With the described setup, the
best results concerning H2 slip as well as surface temperature could be reached with ≥ 2.
Figure 9 shows the effect of self ignition of the unreacted hydrogen.
The tests are carried
out with a hydrogen flow rate of 8 Nl/min and = 3, corresponding to an actual air flow of
60 Nl/min. Just after starting the reaction, the initial hydrogen slip was determined as
18’000 ppm (1.8 vol.%) which is still considerably lower than the lower ignition limit of 4
vol.% hydrogen in air.
As the catalytic coated SiC foam reaches 585 °C, self ignition
occurs inside the porous SiC structure. Hydrogen oxidation now takes place by catalytic
combustion on the platinum coated porous SiC ceramics and to a small fraction by thermal
combustion. This leads to a complete oxidation of the hydrogen and thus reduces the
hydrogen slip in the exhaust gas to values below 50 ppm. At the point of self ignition, a rise
in temperature on the SiC surface can be observed (Fig. 9). The burner plate surface
temperature levels at approximately 850°C, while the glass ceramic surface reaches the
maximum temperature of 600°C
Efficiency tests were carried out according to DIN EN 30-2-1 [7]. This standard deals with
home cooking stoves based on gaseous fuels. The testing procedure consists of heating
3.7 kg of water in a pot with an inner diameter of 220 mm from 20 ± 1 °C to 90 ± 1 °C. The
minimum cooking efficiency by the DIN norm is set to be 52% for gas stoves. To improve
the overall efficiency of the hydrogen stove a heat exchanger was implemented. Incoming
air is preheated via heat exchanger by the exhaust air. Tests have been carried out with
heat exchanger and glass ceramic cover (complete setup) as well as without heat
exchanger and/or class ceramic cover to compare the corresponding efficiencies.
Efficiency tests were done at hydrogen flow rates of 6 Nl/min, 7 Nl/min ( = 2) and 8 Nl/min
( = 2.4) (Table 2). Based on the lower heating value, the efficiency was found to be 59%
without heat exchanger, 66% for the complete setup (with heat exchanger and glass
ceramic) and 70% with heat exchanger but without glass ceramic plate, measured directly
above the SiC ceramics.

Fig. 9: Temperature over time, H2 leakage and self ignition point for a H2 flow rate of 8
Nl/min and = 3

3. Conclusions
The goal of this research to develop and optimize a catalytic hydrogen fueled burner could be achieved. A novel catalytic diffusion burner for hydrogen, based on highly porous silicon carbide (SiC) ceramics and platinum (Pt) as catalyst has been developed for applications like cooking stoves or room heating.
Due to the self igniting effect and the very low hydrogen slip, a high safety standard can be reached. As no carbon is involved in the combustion and the temperature is below 1200°C, no hazardous gases are exposed.
Efficiency over 66% could be reached, which is considerably higher than the standards for conventional gas stoves. The results from the tests conducted throughout this research have proven the possibility of using H2 for cooking and matching the safety, the overall efficiency, performance and convenience of commercially available gas- or electro stoves.
Acknowledgement
We would like to thank the SELF team M. Zimmermann, B. Olsson, S. Machi, Bundesamt
for Energy, Bern, Project Nr. 154485/103401 for the financial support of this project as well
GWM (Austria), V-Zug, Switzerland and Infragas for materials support.
References
[1] M. Bielmann, U.F. Vogt, M. Zimmermann, A. Zuettel; Seasonal energy storage
system based on hydrogen for the self sufficient living unit (SELF), Journal of Power
Sources (electronically published 12-2010)
[2] U.F. Vogt, M. Gorbar, P. Dimopoulos-Eggenschwiler; A. Broenstrup, G. Wagner, P.
Colombo, Improving the properties of ceramic foams by a vacuum infiltration process,
Journal of the European Ceramic Society 30 (2010), pp. 3005-3011
[3] B. Dahm; Experimente und Modellbildung zur diffusiven katalytischen Verbrennung
von Wasserstoff, Fortschrittsberichte VDI, Reihe 6: Energietechnik, Nr. 360, 1977
[2] Stanley I. Sandler; Chemical, Biochemical, and Engineering Thermodynamics, 4th
Edition (2006), John Wiley and son, ISBN 978-0-471-66174-0
[3] Hanson F.V., Boudart M; The reaction between H2 and O2 over supported platinum
catalysts, Journal of catalysis 53 (1978), P 56-67
[4] Mercea J, Grecu E, Fodor T; Heating of a room by use of a hydrogen-fuelled catalytic
heater, Int. Journal Hydrogen Energy 6 (1981) 4, p 389-395
[5] Winter C.J, Nitsch J.; Wasserstoff als Energieträger: Technik – Systeme – Wirtschaft.
(1989), Springer Verlag Berlin; Heidelberg; Newyork, ISBN 978-3-540-73527-4
[6] Siong Victor; Batchelor thesis „Flamless catalytic combustion of hydrogen“, 2010
[7] DIN EN 30-2-1; Haushaltkochgeräte für Gasförmige Brennstoffe, Teil 2.1: Rationelle
Energienutzung, ICS 97.040.20, August 2005
However, if CHC is thought to be employed for heating purposes, silicon carbide should be considered as a support of election due to its high mechanical strength, chemical inertness and high thermal conductivity to prevent the formation of hot spots [20]. SiC has been reported previously as a support for other catalytic reactions such as methane (or methane/H 2 mixtures) combustion and Fischer-Tropsch reaction [20][21][22][23][24][25] but only recently for the CHC reaction [26,27]. In these previous works [26,27], carried out by the EMPA laboratory, a commercial Pt washcoat (supplied by INFRAGAS and usually employed for methane combustion) was supported on clay bound SiC foams and used, in monolith form, as CHC catalyst for the design and construction of a H 2 based cooker. ...
... SiC has been reported previously as a support for other catalytic reactions such as methane (or methane/H 2 mixtures) combustion and Fischer-Tropsch reaction [20][21][22][23][24][25] but only recently for the CHC reaction [26,27]. In these previous works [26,27], carried out by the EMPA laboratory, a commercial Pt washcoat (supplied by INFRAGAS and usually employed for methane combustion) was supported on clay bound SiC foams and used, in monolith form, as CHC catalyst for the design and construction of a H 2 based cooker. This hydrogen burner operates with air- fuel equivalent ratios (λ) in the range 1.5-3.0 ..
Owing to the separate H 2 and air feeding system and the possibility of accurate regulation of the H 2 and air flow, it is possible to modulate the burner temperature very precisely as reported also by Haruta and Sano [14]. By regulating the H 2 and air flow rate and also the H 2 to air ratio, a flameless catalytic combustion process at temperatures well below open flame temperature is reached [48]. A very high cooking efficiency of up to 80% according to the standard testing procedure given in the DIN EN 30-2-1: 2005-08 [49] could be realised [45]. ...