
GO Faster Go Further
Established since 2001
Secure Supplies Group
Understanding
Voltage Pulse Frequency Waveform
Amplitude Attenuation (Voltage Boosting)
Primary Voltage Amplitude Pulse Gate Control
Voltage Threshold & Amp Restriction Levels
GPT Interpretation from: https://stanslegacy.com/books/us-patents/page/gas-generator-voltage-control-circuit-4798661
L-1. Voltage and Current Regulation: The use of a uni-polar pulsating DC voltage is an initial approach to raise the amplitude of the voltage without electron leakage. However, it has a limit up to an amplitude of 4.0 volts. This is represented by level L-1 in Fig. 8.
L-2. Duty Cycle Variation: To further restrict current flow with amplitude voltages above L-1, the duty cycle pulse of the pulsed DC voltages can be varied (as shown in FIGS. 2, 3, and 8). This can help control and limit the electron leakage from the exciter plate which has negative voltage applied. The voltage amplitude limit in this approach is 4.0 volts, as represented by L-2 in Fig. 8.
L-3. Pulsed DC Voltage: The pulsing of the pulsed DC voltage, which comprises switching the voltage on and off periodically, can help in the function of inhibiting electron leakage. The duty pulses have an effective amplitude in inhibiting electron leakage by controlling the force on the electrons around the plate exciter, having the negative potential voltage applied. The amplitude is effective to increase the output gas generation with an upper limit of 5.5 volts, in this instance L-3 of Fig. 8.
L-4. Serially Connected Exciter Plates: Though serially connected exciter plates do permit a higher amplitude of voltage to be applied, it too, has a limitation L-4 of 7 volts. This method allows the positive voltage to be applied individually to each of the outer plate exciters and the negative voltage to each of the inner plate exciters, which increases the surface between the inner and outer plates, thus reducing the probability of an electron breaking free and leaking to the attractive field of the positive voltage plate.
L-5. Use of Resistors as Current Inhibitors: Resistors, such as resistor 60 shown in FIGS. 1 and 5, can act as simple current inhibitors to prevent electron leakage. These resistors can be fine-tuned for specific applications and are connected to each of the plates having the negative voltage connected thereto. They effectively raise the voltage amplitude limit to 8.5 volts before breakdown, as shown at L-5 in Fig. 8.
Beyond L-5. Use of Poor Conductive Material: Using a material that is a poor conductor of electricity, like stainless steel 304L, can further inhibit electron leakage. This material is used in the electron inhibitor, shown in FIG. 7, which is connected between the inner plate (having the negative potential connected to it) and ground. Stainless steel 304L is considered a poor conductor when compared to materials like copper or gold, and can effectively restrict the electron flow, thus reducing electron leakage. This technique removes the upper level of amplitude of the voltage as shown beyond L-5 in Fig. 8. Fine-tuning of the resistive value of the electron inhibitor is achieved by changing the resistive material to binder ratio, and by the use of resistor 75 connected in series.
The varying of the duty cycle of the uni-polar DC voltage pulses is a technique used to control the amplitude of the voltage and thereby inhibit electron leakage. This variation can be periodic or aperiodic:
Periodic Variation of Amplitude (Claim 7):
In the periodic variation of amplitude, the on/off pattern of the duty cycle of the uni-polar DC voltage pulses repeats at regular intervals. This could involve, for example, turning on the voltage for one second, then turning it off for one second, and repeating this pattern continuously. This form of periodic variation can help maintain a certain average voltage amplitude, preventing electron leakage by keeping the voltage within safe limits.
Aperiodic Variation of Amplitude (Claim 8):
On the other hand, in the aperiodic variation of amplitude, the duty cycle of the uni-polar DC voltage pulses changes irregularly or randomly. For instance, the voltage might be on for two seconds, then off for one second, then on for half a second, and so forth, with no consistent pattern. This form of aperiodic variation might be useful in systems where the conditions fluctuate or where a certain level of randomness is beneficial. As in the case of periodic variation, the aim is to maintain an average voltage amplitude that minimizes electron leakage.

Step Charge as a function of Pulse Period
Here we can see the Cell Driver Circuit pulsing a double cell in parallel. The arrangement is powered by a 12V ATX supply.
The Cell Driver's inputs: Vcc and Vee are both B+ 12VDC REG. The primary coil is replaced with the LC load of the cell & a 39mH iron core inductor, either using the centertap or the full coil. (12-0-12 side of a 6:1 stepdown. 120V side at 612mH).
The water in the cell was old well water.
(new tests are needed with fresh and/or distilled water)
Parameters of Test:
Width: 1388 uS
Space: 760 uSF = 1/S
F = 1 / (0.001388 + 0.000760) = 1 / 0.002148 uS
F = ~465 Hz ?Gate Spacing (2466 uS or 2.466mS)
Inductor: 17.5mH (half of a 12-0-12 stepdown at 39mH total)
DMM Measured Resistance 12-0-12: 0.6R each half, and 1.3R full coil
B+ Voltage applied to cell: 12V REG (from ATX supply)
Transformer used as inductor: Jameco Valuepro 67-1242 Center-Tapped Power Transformer, 24 VAC, 48 Watt, 2 Amps, 2.60" H x 4.10" W x 2.50" L
This inductor appears to be playing the role of Vc2.
When I introduce a mutually coupled Vc1 (the other side of the core at 612mH), regardless of phase, all modulation and/or rise is completely dampened.
Too large of an inductance at the Vc2 position (in this specific arrangement),
dampens out all modulation.
Too small of an inductance at the Vc2 position (etc), allows much more of the pulse to be reproduced at the load Vout, and "Cell Saturation" is perhaps reached too soon.
Too large of an inductance in a Vc1 position also significantly inhibits modulation, unless sufficient offsetting capacitance is added in the form of parasitics, distributed coupling or external parallel capacitance.
Perhaps this is the reason for the inverted pulse trains feeding the Cell Driver input. If a constant DC bias during "offtime" is applied, then during the pulse pull down, inductive reversal directed by the diode, is responsible for the higher voltage spikes.
This process cumulatively increases the bias of the cell cathode with each successive pulse by allowing the energy to store in the negative (side) inductance. The voltage will rise (return) up to at least the available source voltage, or higher with the spikes.
Given a higher voltage input, it seems quite possible that the 8XA style variac power supply, with added filtering, could supply the load directly (replacing the 12V REG here), up to 60VDC at least regarding the TIP120 thresholds (100V TIP122).
Utilizing a higher voltage input would presumably result in much higher amplitude spikes, with the same 2.5V threshold, which appears to be the forward voltage drop across the TIP Collector/Emitter junction.
(Edit: Don't use a variac. It will blow something up. Instead, we should look at using a 0-60VDC supply, with an addition 7812 12V Regulator to supply the Vcc/Vee to the Cell Driver.
This will keep everything on the same bonded ground, and safe for operation)
With this operation in mind, and in this configuration, I can now appreciate the design of Max Miller's digitally controlled power supply board, and its inverted output pulsing.
The cell driver TIP120, in this case, acts as a low side switch on the cell, and is rendered safer to operate, by existing electrically further away from the B+ voltage source.
The NPN junction is not subject to a large voltage differential during switching. The voltage dropped across the inline cell and inductor significantly reduces the remaining voltage to be dropped across the junction.

Schematic for arrangement
Edit: Inductor is 39mH and circuit operation used the center-tap for an equivalent inductance of 19.5mH

Cell Driver Circuit
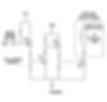
UPDATE: 7/4/22
Swapping out the freshly conditioned new cell, for the old double barrel, and using the same inductance, caused a shift in the saturation limit of the step-charge.
The old cell exhibited almost too much dampening, and significantly less bubbles were the result. Pulse width had to be reduced to levels under 500uS in order to regain the stepcharge.
At which point, the amplitude also suffered, suggesting an adjustment to inductance is required.
More tests are needed with other cells and inductances to determine where the largest headroom (width vs. count) exists, allowing the highest source amplitude possible, to be reached.
Voltage Attenuation
The "9 Stages to Voltage Attenuation" of the VIC
Voltage intensifier Circuits
-
Conventional Power Supply - less than 1V - 110V DC (or equivalent rectified AC)
-
TBD - no mention (believed to be the Gate Frequency & Process)
-
Pulse Train concentrated or "Time-regulated" variable pulse voltage frequency allowing for higher voltage amplitude
-
Resistive wire 430/FR in inductors ( On latter versions 9 to 11)
-
Repetitive Formation & Collapse of Oscillating Magnetic Fields (in Resonant Charging Chokes) allows duplicated Voltage Wave Form (9B) and forms Inductance Coupling (Allowing pulses through, but restricting amps)
-
Preventing Electrical arcing beyond voltage gap thresholds
-
Sequential Gate is varied beyond attenuated voltage control
-
Frequency (Alternator) is varied
-
Varying of Voltage Pulse Amplitude Input
10: Repeated Dual Voltage Pulse-Train
11: Dual Voltage Pulse Train - Duty Pulse Cycling (Increase Pulses Per Second Per Attenuation)
12: Voltage Amplitude is adjusted no further, to keep amp flow to a minimum, once Compounding Action is properly maintained.
13: TBD
14: Varying Gate Switch Circuit (58) to control gas production on-demand
15: Sequentially switching OFF and ON additional Excitors to control gas production on-demand